Multiscale Analysis of Rice Milling Process with Particle Simulations
Klaus Kuboth
17.12.2024
More than 20 million particles in a simulation model
Rice whitening is a critical phase in rice processing, with the challenge being to reduce broken grains. Ansys Rocky software helps to understand the dynamics involved, which are pivotal for optimizing machine design and processing conditions. We talked to Dr. Clément Zémerli, Senior Simulation Engineer at Bühler Group, about how the company manages large scale simulation projects in Rocky and how they use the insights they gain.
Clément, you are a speaker at the CADFEM Conference 2024. Your presentation is entitled 'Multiscale Analysis of Rice Milling Process with Particle Simulation.' Can you please summarize your presentation for those who did not attend your talk?
As a technology partner for the food, feed, and mobility industries, Bühler delivers equipment for rice milling. This is a crucial process for our customers, but also for the world, as billions of people consume rice. One of the biggest challenges in this process is the rate of broken grains, which can be as high as 20%. It's very important for our customers to have a machine that not only reduces the number of broken grains but also aligns with Bühler's sustainability targets. Therefore, we are heavily investing in research and development to reduce the number of brokens.
What challenges were you confronted with?
Particle simulation of rice whiteners is very challenging because we have to calculate the behavior of millions of grains. It is essential to accurately reproduce the rice flow dynamics. While Rocky enables us to achieve this, the real challenge is to develop a method that can predict both the breakage and the degree of milling.
For this, we need not only a robust simulation method but also strong experimental expertise. By combining these competencies, we can make the best use of simulation. We need to extend the current usage of DEM simulation in order to model rice breakage and rice dehulling rates. This requires measurements at the grain scale, including tribological tests and breakage energy assessments. Once developed, the models can be validated through trials conducted at the industrial scale.
Would you say this project was a success?
The project has been a success for us. Firstly, we know now that it's possible to generate a full-scale simulation model for the rice whitener. Secondly, we have gained significantly insights, such as understanding the mechanisms and the influence of process parameters on the machines. We can provide this data to our process engineers, who can directly apply it to optimize the use of our existing machines at our customers' locations. Last but not least, the true measure of success will be evident in a few years when we enhance the performance of new machines based on the data from our simulation project. Ultimately, it is not for me to judge it success; that will be determined by the customer.
General flow behaviour is captured with DEM simulation showing flow patterns around the stones that is observed experimentally. | © Bühler
Okay, and if we talk about size, just to get an imagination, how many particles do you have in your model?
We can work with more than 10 or 20 million particles in our simulation model, but please be a bit patient as the simulation time can take several days to complete. Despite the wait, the wealth of information obtained from these simulations is invaluable. We can get the force between the particles, the contact, the interaction, the stress, providing key insights for our processes. The comprehensive data makes waiting for the simulation worthwhile.
To provide some context, each rice grain undergoes mechanical loading several hundred times in the simulation, and we have millions of rice particles. We then apply statistical methods to extract all the mechanical loading data that the rice grains experience. By combining this with our experimental data on how the rice responds to different loads, we can infer the likelihood of rice grains breaking.
The wealth of information obtained from these simulations is invaluable. We can get the force between the particles, the contact, the interaction, the stress, providing key insights for our processes. The comprehensive data makes waiting for the simulation worthwhile.
Are there some requirements to do simulations like this, or can you just use your traditional or normal hardware?
One of the biggest limitations of particle simulation is computational time. To address this, we aimed to run large-scale particle simulation models in-house, which required having the necessary hardware on-site. For that, we invested in GPUs a few years ago. This was a very important strategic move for us.
Rise brokens estimation is a combination of a) counted contacts sorted into impact energies levels and b) material response data to load. Calculated values of brokens match observations. | © Bühler
Do you see some potential to apply the knowledge you get from that project to other processes at Bühler because Bühler does not only own the machines for rice? Are there any benefits for other processes or machines?
Bühler is a leader in milling solutions, handling a wide variety of grains with extensive range of machines and equipment. The knowledge we build from our rice projects can be extended in the future to other materials such as wheat, maize, and lentils. Moreover, the know-how we are building is not limited to this specific project; it will be valuable for other departments at Bühler as well.
Thank you very much, Clément.
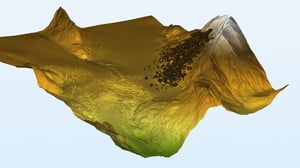
Particles and Flow Meshless
Summarized presentation of new features and enhancements in Ansys with a focus on particle-based methods.
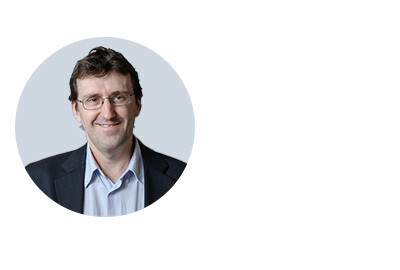
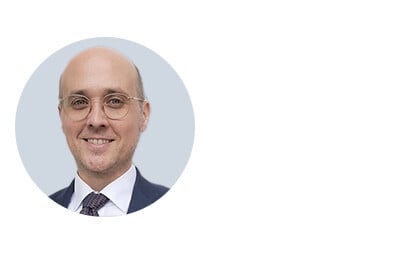