Innovative simulation approach reduces energy consumption of large fans
Alexander Kunz
28.01.2025
Small changes, big impact
Large industrial fans in ventilation systems ensure good air quality in tunnels, halls and spacious buildings. But this consumes a lot of energy – too much. That's why the EU is tightening up the guidelines on minimum efficiency. A current doctoral thesis shows how manufacturers can comply with these guidelines. One key to this is CFD simulations.
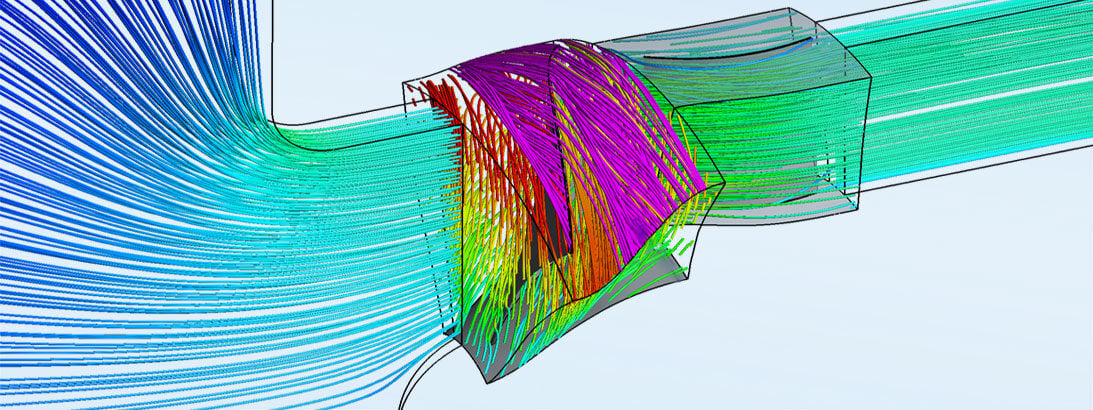
Visualization of the gap flow of a low-pressure axial fan | © Hochschule Coburg
Dr. Manuel Fritsche has developed a new method for the simulation and design of air flows in fans. | © Natalie Schalk / Hochschule Coburg
Dr. Manuel Fritsche studied mechanical engineering at the University of Applied Sciences in Coburg, completed his master's degree and then did his doctorate there in cooperation with the Friedrich-Alexander-Universität Erlangen-Nürnberg (FAU). In the process, he has become an expert in flow simulations. This expertise shaped his doctoral thesis, which he completed with “Magna cum Laude” in March 2024. At its core is an optimization strategy that enables manufacturers of industrial fans to meet the stricter EU Eco-design Directive on minimum efficiency. The EU regulation number 327/2011 is part of the ErP Directive 2009/125/EC and requires a significant increase in the energy efficiency of the systems.
“The systematic increase in the minimum efficiency level poses a technical challenge for manufacturers,” says Dr. Manuel Fritsche. He addressed this challenge in his doctoral thesis, supervised by Prof. Dr. Philipp Epple, head of the Fluid Mechanics Laboratory at the Faculty of Mechanical and Automotive Engineering at Coburg University of Applied Sciences, and Prof. Dr. Antonio Delgado from the Institute of Fluid Mechanics at FAU. The simulation tool used in his dissertation titled “Simulation-driven design and optimization strategy for an axial fan with a guide vane” was the ANSYS CFXTM software. It is the leading software for turbomachinery and was provided by CADFEM, a close sales and technology partner of Ansys.
Proven software – new approaches
Ansys CFX was developed specifically for simulating turbomachinery and has been used for this purpose for decades. This also shows that numerical flow calculations or CFD (Computational Fluid Dynamics) are not a special feature in and of themselves, but rather a standard in fan development. However, the approach pursued by Dr. Manuel Fritsche reveals additional, previously undiscovered potential for particularly energy-efficient operation of axial fans.
Efficiency is more important in operation than in production
For cost and production reasons, industrial axial fans are usually manufactured with three-dimensionally bent blades made of sheet metal of uniform thickness. This is where Dr. Manuel Fritsche's strategy comes into play. Based on thousands of simulations, the behavior of alternative blade designs and their impact on efficiency is tested, i.e. lower energy consumption with at least the same performance.
The previous requirement and minimum production costs are therefore secondary to the goal of maximum energy efficiency in operation. The optimization potential should be determined in the smallest details and the possibilities of Ansys CFX fully utilized.
In the first step, the approach uses an analytical design of the blades based on physical equations, taking into account the total pressure distribution, as well as extensive CFD simulations. In the second step, the results are further improved within Ansys Workbench using a digital multi-objective optimization method (DoE, response surfaces, parameters).
Visualization of the gap flow of a low-pressure axial fan. | © Hochschule Coburg
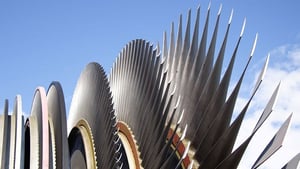
CFD Analysis of Turbomachinery
Learn the practical use of Ansys TurboSystem tools for design, simulation, and optimization of radial and axial flow machines.
High performance from Erlangen
Dr. Manuel Fritsche's strategy goes far beyond the spectrum of traditional simulations, which is made possible by the integration of HPC technology. He was able to access this computing power, which is 120 times higher – approximately 1,000 computing cores instead of the 8 in a standard PC – through the Center for National High Performance Computing (NHR) of the Regional Computing Center (RRZE) of the FAU.
Example: influence of blade design
Using the example of the blade of a low-pressure axial fan, he identified the areas where a redesign would lead to less turbulence and more flow efficiency. Among other things, he used identical designs to examine the influence of the blade length in external areas. It was shown that a longer blade significantly improves the flow pattern, which is reflected in pressure and efficiency characteristics.
Influence of the impeller blade length in the housing | © Hochschule Coburg
Another example is the detailed examination of the gap flow between the rotating impeller and the housing, which, for manufacturing reasons, is unavoidable. With CFD, the influence of the gap height can be analyzed quantitatively and gap vortices can be analyzed qualitatively using corresponding streamline plots.
Both examples show a major benefit of numerical CFD simulation. Even areas that are difficult to access for measurement can be examined in detail.
Influence of the impeller blade clearance on the flow in the blade channel at various operating points. | © Hochschule Coburg
A contribution to climate protection
The new design and optimization process was validated with the help of prototypes from an industrial partner. “The Institute for Prototyping and Model Technology at Coburg University of Applied Sciences created fan prototypes for me using 3D printing,” adds Dr. Manuel Fritsche. As a result of his research, axial fans can now be designed with significantly increased efficiency and optimized operating performance – a contribution to implementing the stricter EU directive.
Since the manufacturing processes for fan blades are becoming ever more flexible, the redesign of the components has hardly any disadvantages in terms of manufacturing costs. This is because 3D-formed blade shapes are easily possible, especially for impellers that are manufactured additively or by injection molding. The strategy developed by Dr. Manuel Fritsche can therefore improve the energy efficiency of fans wherever large ventilation systems are used. This, in turn, addresses the actual core of the sometimes unwieldy EU regulations: it contributes to climate protection.
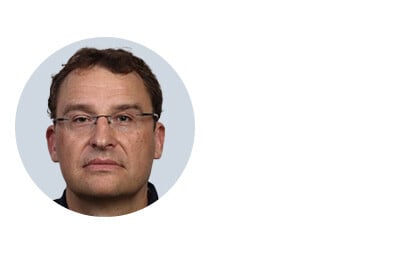
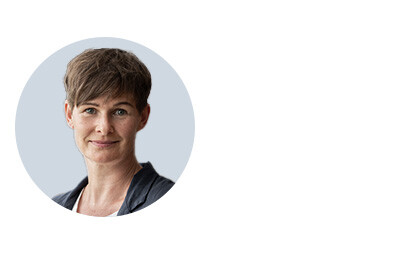
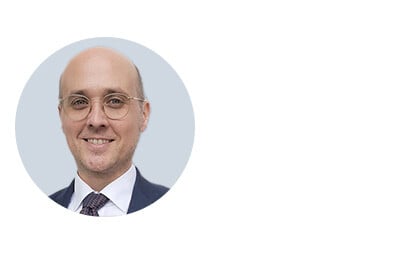