Mechanical-thermal coupled simulation of a brake disk
Gerhard Friederici
18.03.2025
Fast and accurate: hybrid calculation of brake disc heating
The simulation of coupled mechanical-thermal phenomena, as in a brake disk, can take a very long time. A solution in a shorter time can be achieved by implementing a hybrid calculation approach. This involves a purely thermal simulation, with the mechanics being handled by analytical methods.
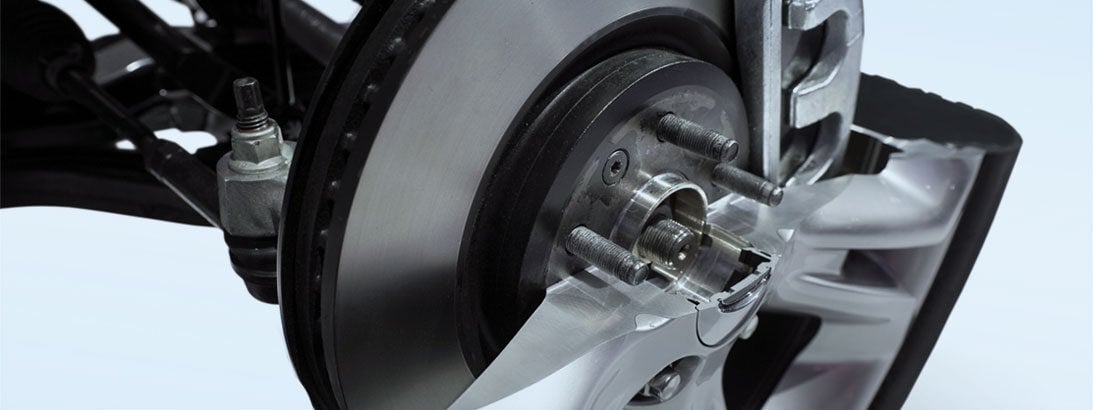
© Getty Images
Rotational energy is converted into heat energy
Generally speaking, the braking process of a mechanically braked brake disc can be explained as follows: Friction linings, which are pressed onto the disc with a certain contact pressure, extract rotational energy from the brake disc and, in accordance with the conservation of energy, convert it (for the most part) into heat energy. This is then released into the environment via the three heat transfer modes.
Coupled simulation models are not rocket science …
To find the best possible settings for the friction linings in terms of material, geometry and positioning when developing such braking systems, Ansys simulation models are useful, as they can determine the resulting temperatures depending on the load. For this application, the physical sub-disciplines of structural mechanics (rotation, contact pressure) and thermodynamics (heat generation through friction, temperature field) must be taken into account in the simulation tools. Since these two disciplines mutually influence each other – for example, through the temperature-dependent friction coefficient of the brake linings – the calculations should be carried out using a coupled simulation model.
Nowadays, setting up such a model – for example with Ansys Mechanical – is no longer rocket science. The necessary settings, loads and boundary conditions can be quickly defined using the user-friendly interface. So far, so good – but after pressing the “Solve” button, the numerics get in the way.
… but the calculation can take a long time
Brake discs rotate at several revolutions per second, which leads to strongly modified FE meshes in structural mechanics during the transient process. This ultimately requires very small time steps for a convergent solution (in the order of milliseconds). However, if a real braking process of a few seconds is to be simulated, it quickly becomes clear that the model construction may only require a short time, whereas the model calculation can be very lengthy (i.e. it may take several hours or even a few days).
In this case, it is advisable to take a closer look and check which aspects must be taken into account in the numerics. The structural-mechanical part of the rotation of a rotationally symmetric disk is not a particularly complex task. The temperature field, on the other hand, is significantly more complicated due to the point heat input.
Understanding and Simulating Technical Friction Effects
Learn to detect and specifically influence friction-induced vibration phenomena.
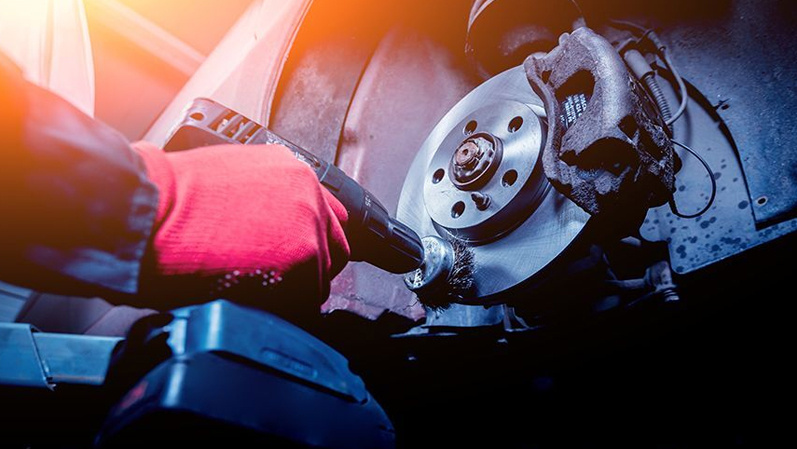
Using programming to analytically integrate structural mechanics
CADFEM chose to use a hybrid approach combining numerical and analytical methods for this task. Additional programming was incorporated into a purely transient-thermal simulation model with an advection term to take the equations of motion of the structural mechanics into account analytically, thus generating heat.
Simulation of heat generation in a brake disk | © CADFEM
The workflow is able to take parametric initial velocities or velocity-time tables, external torques, contact forces, material- and temperature-dependent loss distribution at the friction contacts, as well as velocity-dependent convection coefficients into account. The resulting variables are the usual thermal values (temperature, heat flows) at any time and any location, as well as the rotational speed, the resulting power losses and the total angle of rotation – each over time. So all the relevant variables are present, and the nice thing about this is that this hybrid calculation is about 1,000 times faster than the purely numerical calculation, taking just a few minutes.
A thousand times faster with engineering and simulation know-how
In this case, “lesson learned” means that numerical simulation can be used to analyze (almost) all technical processes. When simulation know-how is combined with engineering know-how, the simulation model can be improved to such an extent, in terms of the required computing times, that the influences of all input parameters can be analyzed and taken into account in the early development phases. This saves a considerable amount of time by reducing the computational effort, but still allows the initial prototypes to meet both the developers' and the customers' requirements.
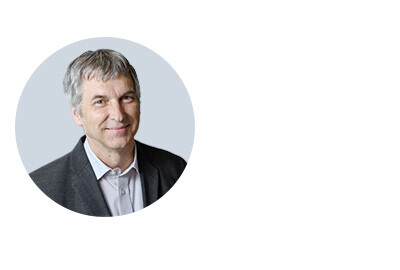
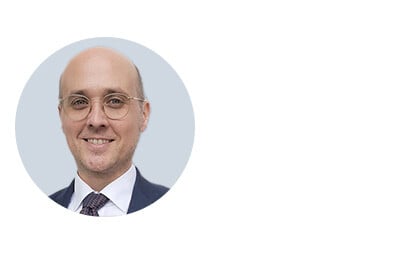