Meshing strategies for explicit simulation
Oliver Siegemund
08.11.2024
Tech Article 24/16 | Who is afraid of the quadratic tetrahedron?
Using a drop-test simulation, we would like to show you that it is not always necessary to defeature your CAD model in a time-consuming manner, because Ansys offers efficient meshing strategies for explicit simulations. Although often frowned upon for historical reasons, tetrahedron elements and in particular quadratic tetrahedron elements can be the solution for thin-walled, complex components. Especially for newcomers to explicit simulation, we recommend the safe route via quadratic elements, global meshing settings and automatic mesh defeaturing.
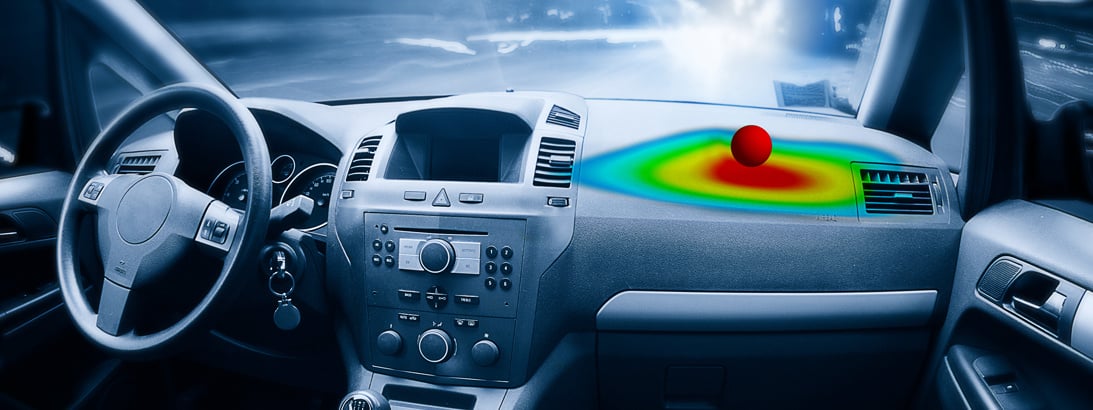
Impact on a car dashboard | © CADFEM Germany GmbH / Getty Images
Integration of the equation of motion and choice of element type
Surely you know that there are different methods for solving the equation of motion. Yet everyone knows that "implicit" is used for linear dynamics and "explicit" for non-linear shock and crash analyses? Well, the fact is that with implicit methods, the time step can be chosen to be large and they therefore show their speed in the low-frequency range. Explicit analyses inherently require a very small time step, so that a wave cannot travel further than one element in one time step. Due to the formulation, however, there is no iterative equation solution, so that it is almost irrelevant whether the problem is formulated linearly or non-linearly. This is why explicit solvers show their strength in the high-frequency range and the non-linearities are virtually given to us as a gift. However, both solvers can basically solve all applications.
You will probably hear a similar number of "myths" about the element types used. For example, it is common practice to greatly simplify models so that they can then be meshed with hexahedra using special techniques. This usually involves many hours of engineering time in order to benefit from fast calculation times. If tetrahedra do have to be used, LS-DYNA users shy away from the quadratic element, as this would halve our time step again and double our calculation time for this reason alone.
And why have we always done it this way? Because the times demanded it! In the early days of (explicit) simulation, we simulated on crays using punched cards and stored the results on magnetic tapes. At that time, engineering time was cheaper than simulation time and storage space was an expensive commodity. Today, explicit simulation is available to a wide range of engineers. Our models, e.g. complex injection molded components, can only be simplified with enormous effort. This means that efficient simulation today can also mean preparing models less. This strategy needs powerful meshing tools with many practicable defaults and automatisms, but also tetrahedra with quadratic Ansatz functions. In this article, I would like to use an easy-to-understand example to demonstrate sensible meshing strategies and raise awareness of the correct element type.
Different level of complexity | © CADFEM Germany GmbH
What we should know about drop test and impact simulation
In a drop test, an object is dropped from a certain height to examine the effects of the impact and ensure that the object can withstand the loads. A drop test is therefore used to check the safety and reliability of a product and to make possible improvements to the design or materials. Sometimes, however, the component is clamped and a test specimen is dropped. This type of (reverse) drop test leads to a high level of reproducibility and therefore comparability of the test. The energy applied can be precisely controlled via the mass and speed of the impactor. In the automotive sector, for example, a head impact could be simulated in this way.
An impact simulation is based on a few and simple assumptions. The component or the assembly to be examined is usually firmly clamped. Caution: ask yourself whether this is permissible? The impactor is usually modeled as a rigid body and is given an initial velocity. Remember that the fall does not have to be simulated, but can be replaced by an initial velocity. This can simply be calculated as follows from the energy balance:
You can therefore remember that a drop height of h=1m results in v0=4.429 m/s . Finally, you need to decide for the correct end time. In our example, 20ms was sufficient. However, this is highly dependent on the stiffness of the structure and the energy of the impactor.
Last but not least, a brief note on mesh fineness. It is often a matter of the pure deformation behavior of the structure and the (holding) forces. In this case, a rather coarse mesh should be sufficient and must be able to represent the stiffness and vibration behavior alone. If stresses or, for example, plastic strains play an important role, additional local refinement is required. The result variables vary from application to application and depend on the specific questions you pose to the simulation. Do the fixings "clip out" or do pins tear away from the structure?
Model set up of an impact simulation | © CADFEM Germany GmbH / Model: Grabcad
The right meshing for explicit simulations in Ansys LS-DYNA
If you deal with explicit simulations, you will notice that some things are different. For example, in Ansys LS-DYNA, a quadratic displacement Ansatz does not necessarily mean elements with midside nodes. There are also a number of elements that have been trimmed for speed for very specific load scenarios. Have you ever heard of mass scaling in FE models? Since the calculation time step in the model is based on the smallest element, the speed of sound is minimized by locally increasing the density, thus maximizing the permitted time step. Finally, it is important to understand that explicit meshing is more than just meshing and is an iterative process. The user has to find an efficient balance between meshing effort, mass scaling, required result quality and computation time.
Meshing workflow of an explicit | © CADFEM Germany GmbH
For me, the following method has worked quite well. I start with a coarse mesh and get the model "running". I can set the end time on this model and also check the boundary conditions. Once I have a stable model, I can refine the mesh to such an extent that the displacement field and the dynamic behavior are correctly shown. Finally, I refine local points for better resolution of the local stiffness or for local evaluation of the stresses and strains. I adapt the first mesh to the geometry and numerics and adhere to the following empirical values. An aspect ratio of 1-3 to a maximum of 1-5 should not be exceeded. For thin-walled components, 1 element across the thickness is usually sufficient; quadratic elements are recommended (Tet4 or Tet16).
Proven global settings | © CADFEM Germany GmbH
10-15 years ago, when I started with explicit simulations, I also spent hours and days simplifying geometries, removing radii and cutting up components in order to generate fast hexahedron meshes, but nowadays I often take a much more pragmatic approach. Although a good tetrahedron mesh takes longer to calculate than an equivalent hexahedron mesh, it is generally easier and quicker to generate and is in no way inferior to the hexahedron in terms of the quality of the results. In addition, tetrahedra can be applied to the most complex geometries and global settings are often sufficient to control the entire mesh. Furthermore, I am not a fan of reaching the goal quickly but "imprecisely". I prefer to let the model run a little longer with quadratic elements, but I can rely on a better quality of result.
Quick Reference Guide (QRG): Special meshing requirements for explicit dynamics
The QRG provides you with an excerpt from our training course “Practice-Oriented Meshing in Ansys LS-DYNA”. Practical knowledge for quick reference in your day-to-day work, formulas, definitions, menu commands and short instructions in a compact format. Are you interested in the entire training course on this topic? You can find all the information here!
Download QRG for free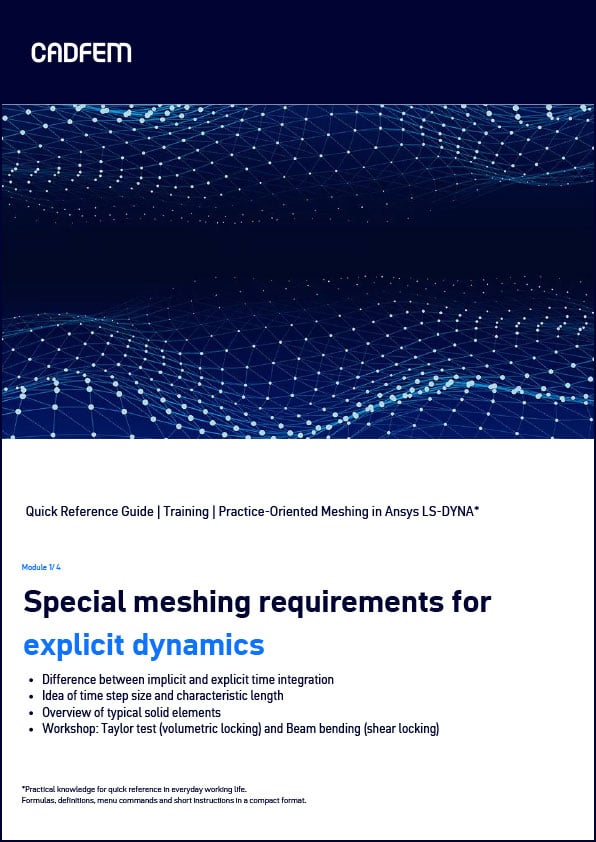
Crash, drop, deformation: simulation of highly non-linear tasks
LS-DYNA is suitable for simulating nonlinear processes with large deformations, stability problems and the most complex contact scenarios
Impact simulation of a vehicle dashboard
As an example, let's take a look at an impact on a vehicle dashboard. The mass 1kg falls from a height of one meter onto a right "soft" and compliant point, so that we generate a bending-dominant load case. As a result, we use the displacement of the impactor. The structure is meshed with the previously shown default settings with ~420,000 tetrahedron elements.
Four element types are compared:
- Tet10: linear, Default
Fast but very stiff element, should only be used for materials with a low Poisson's ratio. - Tet13: linear, additional pressure degree of freedom
Suitable for materials with a higher Poisson's ratio (hyperelastic or plasticity) -
Tet4: quadratic, without midside nodes, additional rotational degree of freedom
Recommended for thin-walled structures -
Tet16: quadratic, with midside nodes
Linear and quadratic tetrahedron in LS-DYNA | © CADFEM Germany GmbH
The difference in the element formulations is clearly recognizable in the diagram. A good 30% deviation in the displacement behavior of the impactor separates the inferior Tet10 from the superior Tet16. The (quasi) quadratic Tet4 also performs quite well, but deviations are visible. Tet10 and Tet13 give similar results, with Tet13 designed for scenarios with Poisson’s numberclose to 0.5 (hyperelasticity or plasticity). The additional degree of freedom for the hydrostatic pressure therefore offers hardly any advantages in the bending-dominant load case. With the same mesh for Tet10, Tet13 and Tet4 and the same number of nodes for Tet16, there are the following differences in calculation time (in relation to Tet10): 1.6 for Tet13, 1.75 for Tet4 and 9 for Tet16. Since Tet16 has more nodes, we can mesh twice as coarsely, which results in a factor of only ~5.
Displacement field of the vehicle dasboard | © CADFEM Germany GmbH / Model: Grabcad
Comparison of different element types | © CADFEM Germany GmbH / Modell Grabcad
Of course, you can also achieve good results with Tet10. But unfortunately you have to mesh extremely fine. In our example with 3 elements across the thickness, we end up with 30 times as many elements as before!
Conclusion: Tet10, the standard tetrahedron element, calculates the fastest, but has the greatest deviations. Tet13 and Tet4, both with special properties, are suitable for certain load scenarios and offer a compromise between calculation time and quality of results. However, the user must know which element is suitable for which scenario. Tet16 takes longer to calculate, but delivers the best results. Don't forget that you can also use coarser meshing while maintaining the same quality of results.
Convergence study on Tet10 und Tet16 | © CADFEM Germany GmbH / Modell Grabcad
Summary and recommendation
Are you an Ansys Mechanical user taking your first steps towards explicit simulations? Do you work with complex, possibly thin-walled components? Then the following points might be helpful for you. Meshing for explicit simulations is often an iterative process. As in other types of simulation, a suitable mesh density must be defined in order to achieve the desired results with the desired accuracy.
In addition, time stepping and mass scaling must be considered to ensure stability and efficiency. Tetrahedral meshes can usually be generated with a few global settings, and defeaturing can be carried out by the mesher without great effort (mesh defeaturing)
Quadratic elements should be used for thin-walled components. Since the default linear tetrahedral elements in LS-DYNA are designed for speed and not accuracy, users should switch to quadratic elements.
Elements without midside nodes but with additional degrees of freedom (Tet4) can offer a compromise between speed and accuracy. These recommendations aim to improve the efficiency and accuracy of your simulations and help you achieve the best possible results without compromising the stability and efficiency of the simulation. By using the right elements and meshing methods, you can ensure that your simulations are both fast and accurate.
Users with many years of experience should regularly review their established workflows and approaches. CAD models and hardware devices improve over time. Does it still make sense to invest x-days of engineering time in defeaturing and creating hexahedral meshes when good tetrahedral meshes can be created almost at the touch of a button? If accuracy is paramount, why do we avoid quadratic elements? Properly prepared and used in a targeted manner, they provide more accurate predictions, even if they require more simulation time. It is worth questioning your own methods and adapting them if necessary in order to benefit from advances in simulation technology.
Training on the topic
-
Practice-Oriented Meshing in Ansys LS-DYNA
In this training, you will learn how to mesh complex, real-world geometries with a few manual steps (semi-automatic). The focus is based on meshes that meet the requirements for explicit simulations.
-
Intensive Workshop: Structural Mechanics
A must-have for all structural mechanics: After this workshop, you will look at your models with different eyes - guaranteed.
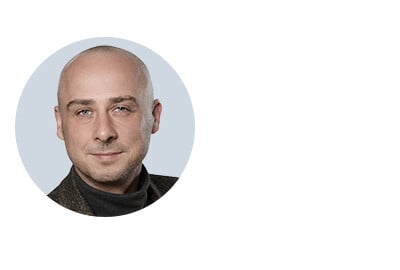
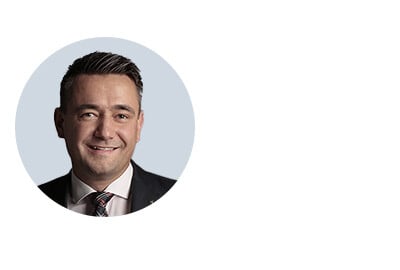
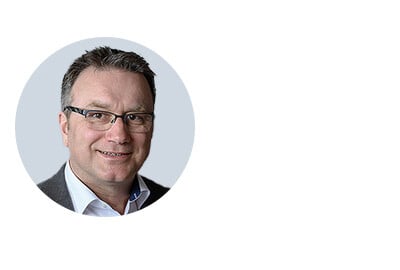
Technical editorial
Dr.-Ing. Marold Moosrainer
Head of Professional Development
+49 (0)8092 7005-45
mmoosrainer@cadfem.de