Particle simulation leads to optimized tribological properties
Gerhard Friederici
02.07.2025
Better surface finishing thanks to the stream-mass finishing process
Surface finishing using mass finishing reduces friction and wear and increases component strength. Simulations with Ansys Rocky can be used to optimize these in a cost-efficient manner. An improvement of 60 percent in bending fatigue strength was achieved by introducing residual compressive stress in a gear wheel processed using stream finishing.
Schalter sind standardisierte Serienprodukte. Das beschriebene Projekt wurde am Schaltwerk des Modells 506U durchgeführt | © JUNG
The virtual modeling of production processes is becoming increasingly important. This also applies to mass finishing processes, which are used as surface finishing processes to improve the tribological properties of components. Unlike conventional FEM or CFD methods, DEM uses independent particles that can move freely and separate from each other. At each time step, the interaction of each particle with potential neighboring particles and boundary walls is calculated. Each movement is accurately recorded based on factors such as stiffness and velocity of movement. This simulation method can take complex particle shapes into account as well as simple spherical shapes.
Stream finishing process of OTEC
OTEC Precision Finishing Solutions GmbH has further developed immersed tumbling to include stream finishing (SF). Stream finishing technology involves workpieces that are clamped in a holder and lowered into a rotating container filled with a grinding or polishing medium. In addition to this rotating container, the workpiece itself also rotates independently around its own axis, which increases the finishing possibilities.
The immersion depth and the immersion angle serve as central parameters of the finishing process. Using further process parameters, the movement of the abrasive particles can be flexibly adapted to the requirements of the respective workpieces. The friction energy is generated by the pressure and the movement of the granulate relative to the workpiece. This energy input during stream finishing is beneficial for surface conditioning and enables a microstructure change induced by shear stress.
Meaningful load cases for DEM validation
Parameter calibration is necessary to ensure correct particle behavior. Determining the static and dynamic angle of repose are established methods to calibrate DEM model parameters such as dynamic and static friction coefficients. However, test cases specific to mass finishing should be used that have contact pressure and similar relative velocity as the target application. In this case, the attacking torque on the workpiece was validated for various container velocities and workpiece positions. A good agreement with a relative error of about 10 percent could be achieved.
60 percent improvement in bending fatigue strength
Together with the Stellantis Research Center in Turin, the introduction of residual compressive stress in a stream finish processed gear was examined. A process, which was initially not suitable, was successfully optimized in order to achieve higher residual compressive stress. An improvement in the bending fatigue strength of 60 percent was achieved.
Helical gears can exhibit an effective pumping effect of the granules through the rotation of the workpiece holder. The interaction between the workpiece and the moving granules introduces a high level of frictional energy. This also changes the microstructure, causing grain refinement to a nanocrystalline edge layer, which helps to reduce surface wear.
Pumping effect at the gear wheel: particle movement trajectories within 0.03 s | © OTEC
The image of the simulation of the gear wheel – filled with the granules between the tooth flanks – illustrates the efficiency of the pumping effect. Due to the rotation of the gear wheel around the axis of the workpiece bracket, a high translational velocity of the particles is recorded. However, the particles clearly do not remain stationary in the tooth gaps. The trajectories of these specific particles for the subsequent 0.03 seconds of the simulation are sketched here. In this short time, the particles leave the spaces between the teeth, creating a relative velocity within the spaces.
Steady state for velocity is quickly reached
The simulation is carried out until a steady-state flow of the granulate filling in the container is achieved. The relative velocity that has been calculated is then compared with the product of normal stress and relative velocity (P x V). This product combination is useful for evaluating local process effectiveness. If one of these factors is zero, no processing is taking place at the corresponding point on the workpiece. The variables are averaged over a simulated process period of one second. This duration is considered sufficient since multiple tool rotations take place within this period.
The simulation was carried out over a total period of 2.5 seconds. A rapid adjustment to a stationary state is evident for the velocity component. By contrast, the pressure build-up is slower, due to the time required for the complete formation of the granulate wall.
Gear wheel and bracket immersed in seven million particles; section of the flow in front of the workpiece | © OTEC
To validate the simulation, the residual compressive stress on the gear wheels was compared with optimized and non-optimized finishing processes. A significant increase by a factor of 2.6 was observed directly at the surface for the optimized process.
With simulation, no experimental trial-and-error process is needed
Conclusion: The potential of Rocky DEM simulation as a tool for improving stream finishing technology has been demonstrated. By using DEM simulations, manufacturing processes can be optimized in a cost-effective manner. In the case of mass finishing described here, the operating parameters are optimized without the need for an experimental trial-and-error process. This means that individual customer requirements and geometries can be taken into account in an even more targeted way than before, and product quality can be improved overall. This advantage will continue to grow in the future with increasing computing power – and thus with accelerated simulations.
Surface Finishing of the Future
Learn in Florian Reinle's presentation how to use DEM simulation for optimal results in surface finishing.
Get the presentation now!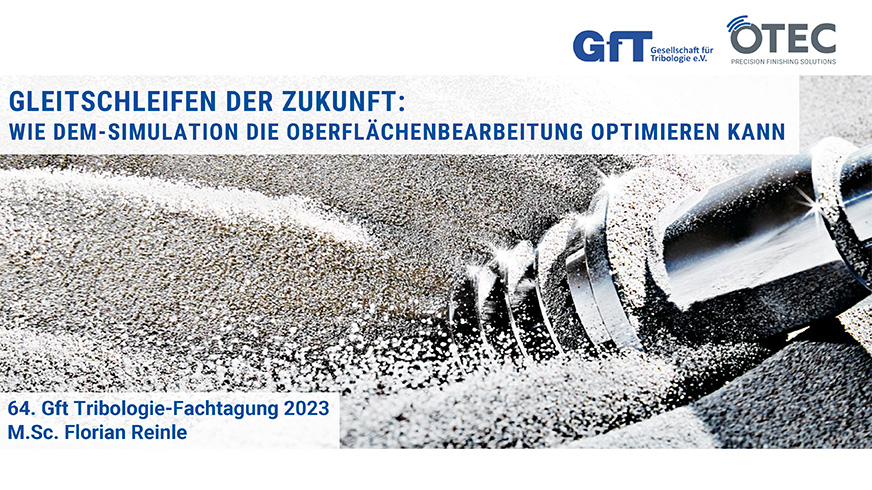
Ansys HFSS
Industry standard for determining the radiation and transmission behavior of high-frequency electromagnetic fields.
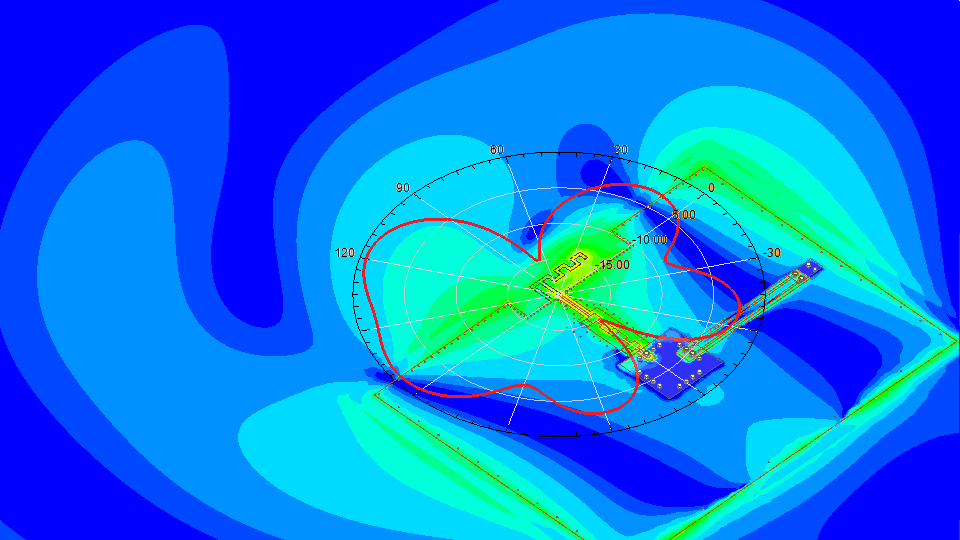
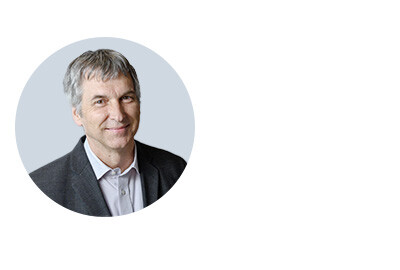
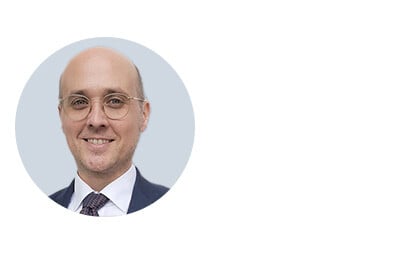