Simulations to minimize the noise emission of electric drives
Gerhard Friederici
26.11.2024
Development of methods for comparing the results of different simulation approaches
Automotive supplier Valeo analyzed and compared various simulation methods that can be used in the vibroacoustic simulation of electric drive axles. This allows the methods to be used in a more targeted and standardized manner, reports Christian Ehrlich, NVH Expert at Valeo E-Automotive Germany.
What was your objective in comparing the various simulation methods?
Our aim was to use the simulation methods that we use for the vibroacoustic simulation of our electric drive axles in a more targeted and standardized way. We want to use Ansys to calculate the radiated sound power based on the surface vibration.
In addition to the FEM (the finite element method), we also use the BEM (boundary element method) as well as the ERP (equivalent radiated power) and LPM (the lumped parameter model). We use both established and niche methods that we have discovered for very specific applications.
Our engineers should always choose the method that leads to quick results with particularly little effort, while of course also meeting the accuracy requirements. This means that our choice of simulation method must always fulfill the desired balance between accuracy and speed.
What advantages do you hope to gain from the standardization that comes with method development?
Our standardization efforts are intended to simultaneously meet two fundamental requirements: to minimize workload and, of course, to provide reliable quality assurance. Since development, and thus also simulation, is international at Valeo, it is important for us to standardize our simulation methods across all locations. This is the only way we can ensure that the simulation is carried out in the same manner everywhere.
In terms of method comparison, we are now at a workable level. This means that we have a good description of how to apply each method. We can give this to the simulation engineers to use as a guide. Of course, there is still room for improvement when it comes to the accuracy of the work instructions. We have laid a foundation, but when it comes to developing methods, you are never one hundred percent finished. For example, we want to work out an even better distinction between BEM and FEM when applying the boundary elements. I can also imagine that the use of artificial intelligence, for example, could take the speed potential to another level.
Can you tell us a bit about the effort and process involved in method development?
Of course, method development is only one aspect of my work. My work focuses on coordinating simulation in day-to-day project business in order to support project validation for our drive axles.
Overall, however, we have invested a lot of time in method development and standardization. We have brought students on board and have dealt with this topic in the form of master's theses, among other things. We also obtained data from ongoing projects where some methods are already in use. The largest block of use cases are standard applications. Here, we see enormous potential to relieve simulation engineers of time-consuming work by automating much of the setup. However, there are still many more tasks that await us.
What other company departments and locations were involved in the project?
I work at the Erlangen site. Our primary responsibility here is for the entire drive axle. This includes the engine and transmission as well as the power electronics. In addition, our transmission specialists in France carry out similar simulations. We are supported by large service centers in China and India with a great deal of expertise, as this is where much of the information from all product areas comes together.
How do you intend to continue automating simulation in the future?
We currently have two objectives in this regard. First, we want to provide our simulation engineers with the best possible support. This means significantly reducing the workload for them in the Ansys Workbench environment. To achieve this, we will further automate the workflow, including report generation, in order to speed up the simulations.
We also want to reduce the workload for simulation engineers by, for example, allowing design colleagues to take on simulation tasks. Ansys Discovery is the ideal tool for this. It allows them to generate an initial assessment or overview of the usability of their ideas themselves.
What expectations do you generally associate with the expansion of simulation tasks beyond the circle of specialists?
In addition to reducing the workload of simulation engineers, the aim is to create a more comprehensive understanding of simulation tasks. This will only work if the existing self-imposed restrictions on simulation in development and design are lifted. The questions and requirements for the simulation department can then reach a higher level and be formulated in a more targeted manner. This allows everyone involved in the project to learn step by step.
I imagine that many design variants that are considered never even reach the simulation stage. Instead, they are immediately rejected by the designer. However, if they could quickly create these variants with Discovery on their own computer and examine them themselves in just a few minutes, then some of these new viable ideas would certainly flow into the designs, which, in turn, would lead to more innovations.
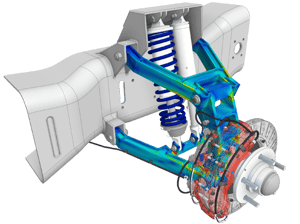
Ansys Discovery
Rapidly explore multiple development concepts with interactive real-time simulation. Experiment in seconds, reliably validate ideas.
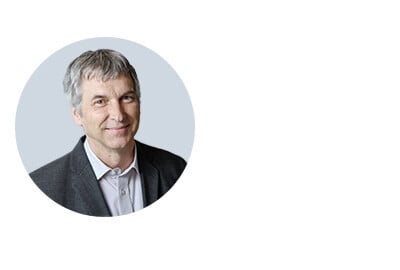
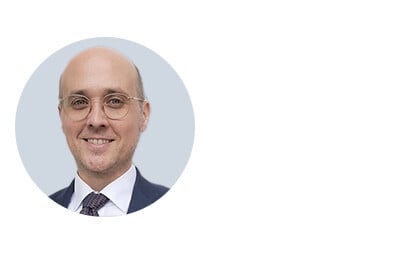