Using Ansys Rocky to optimize silos for uniform discharge
Jan-Philipp Fürstenau
08.05.2025
Particle simulation ensures uniform resting times for molding sand in the silo
Together with CADFEM, a manufacturer of molded sand silos was able to solve problems associated with discharge. The silo was optimized with Ansys Rocky in order to achieve uniform discharge over the entire length of the silo. This ensured uniform resting times for the full contents of the silo.
Molding sand stored in textile silos for reuse
Sand casting is mainly used in the production of larger components. This also means molding sand in large quantities. But what happens to the sand after casting? The molding sand is then stored in silos where it must rest until the next use. Clumped sand and any metal residue is sifted off beforehand. The binder contained in the sand can lead to problems during support and transportation in the form of bridging and adhesion.
Special textile silos are available for this purpose, which mobilize the material through the soft silo walls and prevent unwanted solidification. Nevertheless, when the molding sand is removed from the silo using a conveyor belt, it is removed unevenly along its length. This leads to varying resting times for the molding sand and thus to irregular material behavior during reuse.
How is a uniform silo discharge achieved?
Due to various weight and installation space constraints, variable slide systems, which are used for similar problems, are not an alternative here. This is because the additional weight associated with the textile silo would be too high and the available design space would often be too small. Therefore, a static solution with a low weight and small design space had to be developed to even out the silo discharge.
CAD geometry of the simulated textile silo with component designation. | © CADFEM Germany GmbH
The poor flow behavior of the molding sand to be conveyed makes it difficult to calibrate the bulk material by eye. For this reason, Schwedes + Schulze Schüttguttechnik GmbH commissioned measurements using a ring shear cell for a high-quality calibration of the bulk material. Using this calibration data, the model for the particle simulation of the bulk material could be reliably adjusted.
After calibration, the initial state of the silo discharge was recreated in the DEM simulation with Ansys Rocky in order to reproduce the discharge problem that occurred. This test was immediately successful, so that work could begin on improving the molding sand discharge.
Maximum deviation was reduced from 47 to 8 percent
In collaboration with the silo manufacturer, CADFEM pursued seven different approaches within just a few days in order to achieve uniform discharge over the entire length of the textile silo and thus ensure a uniform resting time for the full contents of the silo. Following initial tests, one variant proved to be particularly promising and was subsequently developed further. Here, the fine adjustment in the field is realized using a slider, which was already present from the outset. With the final variant, the average deviation from the ideal trigger could be reduced from 27% to 5%. The highest deviation was reduced from 47% to 8%.
Observation of the sile discharge, in which the particles are colored layer by layer at time t = 0 sl. Left: Stratification at t = 0 s; center: Stratification after one minute of discharge in the initial state. Right: Stratification after one minute of discharge in the final variant of discharge optimization. | © CADFEM Germany GmbH
The silo manufacturer chose simulation to solve the problem, as the conversion of four silos (40 tons of sand each) at the customer's site involved a lot of work. If the trial-and-error method had been used, the conversion would not have been economically feasible due to the costs and machine downtime.
Picture: Averaged tangential tension in the surface of the conveyor belt due to bulk material friction. The peak tension could be halved by making the discharge uniform | © CADFEM Germany GmbH
Simulations identify problems as early as the project planning stage
By simulating the silo discharge, the flow problem of the molding sand observed at the customer's site was simulated and a solution was found that could be implemented with low weight and a reduced design space. If the simulation had been carried out during the project planning stage, the problem would have been identified in advance and could have been rectified before production.
In addition, the simulation of other sands or similar bulk materials with specified flow properties and wall friction angles can now be checked in advance. This makes it quick and easy to identify the areas in which the geometry found can be used in order to incorporate it into the product range as a standard solution.
Ansys 2025 R1 – CADFEM Tips – Particles and Flow Meshless
In this webinar you will receive a compact overview of the innovations in Ansys regarding particle-based methods. Applications include particle-laden flows, bulk material dynamics, and free surface problems.
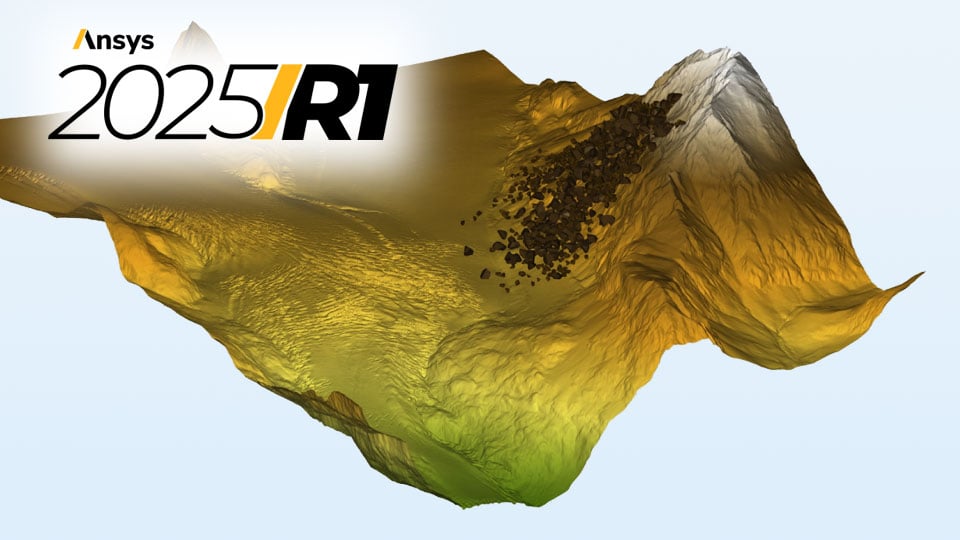
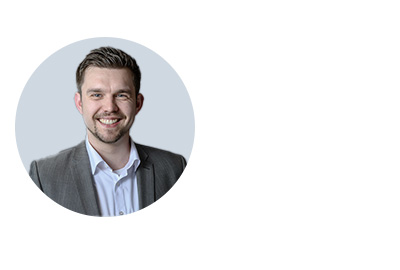
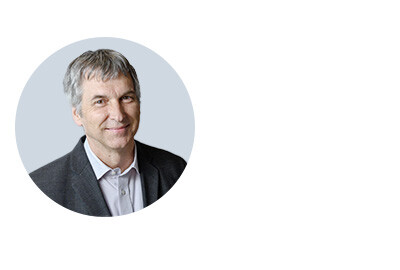