Ansys Rocky: Accurate Simulations through Bulk Material Calibration
Jan-Philipp Fürstenau
09.05.2025
Tech Article 25/04 | Why Guess When You Can Calibrate?
In bulk material simulations using the Discrete Element Method (DEM), precise calibration is essential. Since physical prototypes are often unavailable, direct comparison with experimental data is frequently not possible. However, with proper material calibration, reliable predictions can still be made, enabling effective design and optimization of equipment.
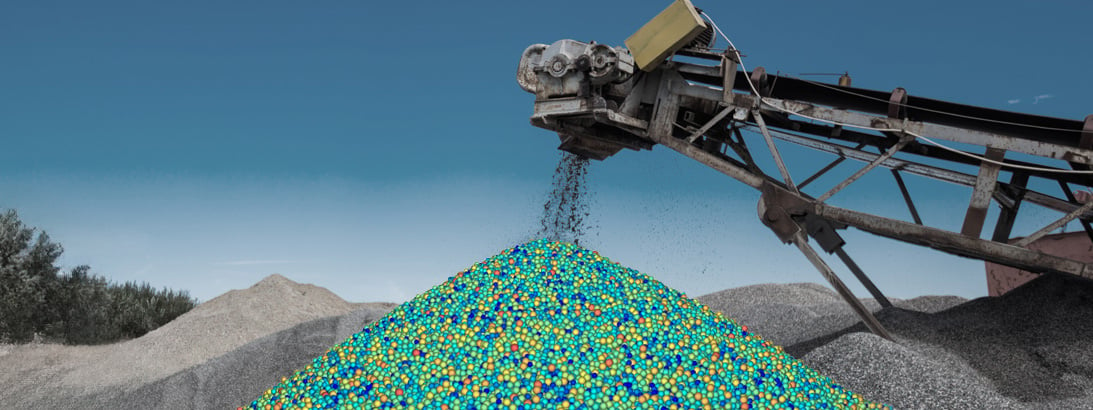
Bulk material | © GettyImages / CADFEM Germany GmbH
Why Is Calibration Essential in Bulk Material Simulation?
While the question of model calibration in structural and flow simulation is usually only of interest for advanced material models and academic issues, calibration plays a role in every quantitative analysis in bulk solids simulation using the Discrete Element Method (DEM). It is less about the physical models and their ability to represent reality than about the correct setting of the model parameters to represent the respective material behaviour.
The reason for the need for calibration are two peculiarities of the DEM:
- The contact properties to be calibrated are microscopic in nature, while the observed bulk solids phenomena are macroscopic (e.g. angle of repose and flowability) Therefore, models cannot be adjusted directly to the observed variables. Such models do exist, but the specific setting limits their applicability.
- The behaviour is based on many input parameters, which have varying degrees of influence. For example, the static angle of repose is mainly influenced by friction and rolling friction. De-pending on the bulk material, attractive forces or the particle shape may also play a role.
The material models and the microscopic material parameters result in the macroscopic bulk material properties, such as the angle of repose | © CADFEM Germany GmbH
From repose angle test to ring shear cell
As the simulation of large systems for the calibration of bulk solids properties is associated with a high computational effort, it has become common practice to carry out the calibration with laboratory equipment. This involves using existing equipment that is otherwise used to experimentally determine bulk solids properties. These laboratory devices can be simulated exactly, which keeps the additional modelling effort to a minimum. Examples of this are the ring shear cell or the static and dynamic an-gle of repose test.
However, standardized tests are only a well-studied possibility, not a necessity. Any test that can be used to determine bulk solid properties is suitable for calibrating a virtual bulk solid. This means that even self-developed tests can be used without any problems. Since the calibration simulation must be carried out more frequently (until the desired material behaviour is achieved), sufficiently small cases should be considered - this applies both spatially and temporally. In other words, observing a system over hours is not suitable for calibration, whereas a laboratory device with a measurement over a few seconds is optimal for several iteration steps of material calibration.
Examples of standardized bulk solids tests. Left: static angle of repose; center: dynamic angle of re-pose; right: Ring shear cell | © CADFEM Germany GmbH
How do I select the right calibration method?
When selecting the calibration method, the load condition on the bulk material and the requirements for the quality of the results play a role. For simple comparative simulations of material deposition in a silo or the free flow of rock in chutes, the determination of bulk density and static angle of repose based on a data sheet and images may already be sufficient. For more demanding simulations, such as the precise prediction of a newly developed system for a particular customer material, automated, detailed calibration tests should be used. For example, the dynamic angle of repose test or the ring shear cell can be used here.
Regardless of whether you opt for an individual or a standard test for calibration, it is important that the test is physically close to the application to be simulated. Here are some examples:
- For sedimentation processes, such as filling silos or bins, the static angle of repose test is the most obvious choice.
- For free-flowing bulk materials without compression, such as in conveying systems, the dy-namic angle of repose test or the ring shear cell with low compression are available.
- For bulk materials flowing under compression, such as in a silo outlet, the ring shear cell with suitably set pressure is the best choice.
An example of the successful application of bulk material calibration with the DEM is the following example of the discharge of molding sand from a trough silo. Initial simulations with literature values showed that the discharge behaviour was not accurate enough. After a flowability measurement by Schwedes + Schulze Schüttguttechnik, the material could be precisely calibrated. Calibration was carried out using the ring shear cell, which is shown as a virtual workflow in Rocky (see illustration). The wall friction of the moulding sand was then calibrated with the silo materials and the overall be-haviour was validated using the static angle of repose.
Calibration workflow of the ring shear cell in Ansys Rocky. Top: Input fields for calibration identical to real test; bottom: calibration result plot. | © CADFEM Germany GmbH
Quick Reference Guide (QRG): Particle Simulation Using the Discrete Element Method in Rocky
The QRG provides you with an excerpt from our training course “Particle Simulation Using the Discrete Element Method in Rocky”. Practical knowledge for quick reference in your day-to-day work, formulas, definitions, menu commands and short instructions in a compact format. Are you interested in the entire training course on this topic? You can find all the information here!
Download now!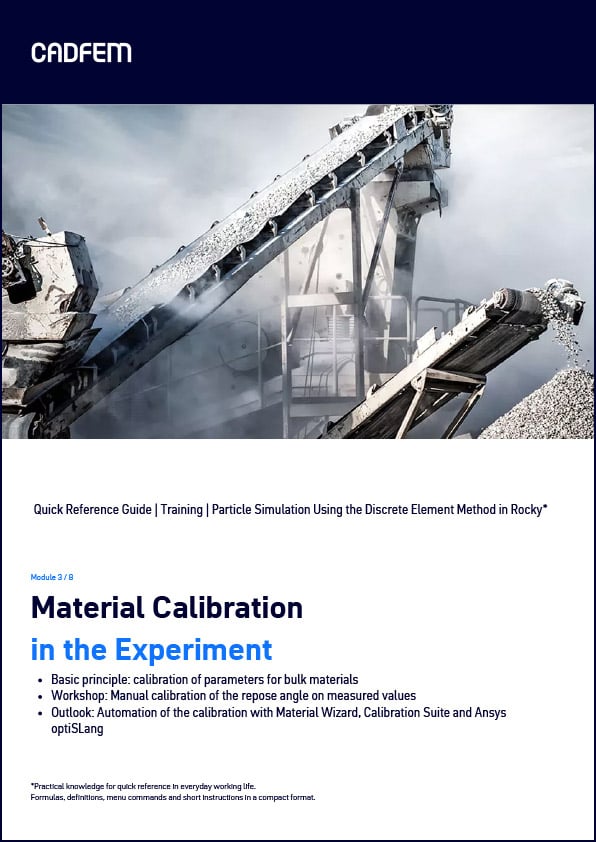
Calibration for real or generic bulk solids?
Once the material behaviour had been reliably adjusted and the quality of the results was convincing, the optimization of the trough silo could begin. A comparison of before and after calibration can be found in the figure below. Different variants of discharge saddles and cross-section reductions were virtually designed and tested until an outlet was found that matched the material and enabled uniform discharge. More details on the application of the trough silo can be found in our CADFEM Insight.
Simulation also creates unprecedented freedom: a material does not necessarily have to be based on a real bulk material. Generic bulk solids can be used to design systems for a range of flow properties, for example. At the same time, it is possible, for example, to check the influence of different densities on the performance of a machine while maintaining the same flowability. Simulation and calibration are not limited to pure flow behaviour. Segregation, caking or flow interactions can also be calibrated and simulated for real and generic bulk solids, to name just a few examples.
Would you like to calibrate your bulk solids simulation precisely - even without complex prototypes? Then secure your place now in our Rocky seminar on particle simulation and learn how calibration works in a practical way. We will also show you the entire range of DEM applications and cover not only observable variables in tests, but also non-measurable variables such as mixing quality in a mixer, wear before it actually occurs, particle loads before they lead to grain refinement and blockages before they trigger a machine standstill. It's worth taking a look: Partikel simulation in Rocky | Seminar
Comparison of the uncalibrated and calibrated bulk solids based on the initial condition of the trough silo to be improved. | © CADFEM Germany GmbH
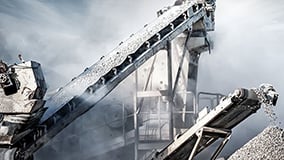
Training Tip
Particle Simulation Using the Discrete Element Method in Rocky
Rocky DEM is an ideal tool for the analysis of many mechanical process engineering applications.
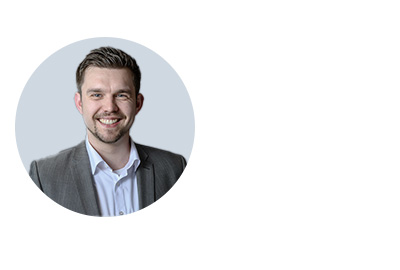
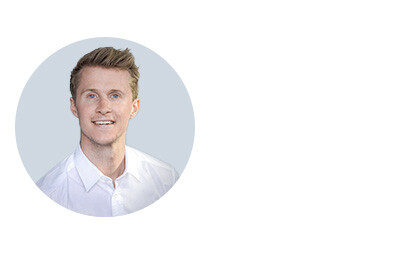
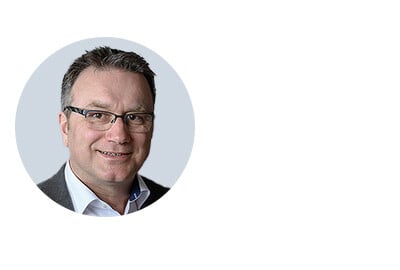
Technical Editorial
Dr.-Ing. Marold Moosrainer
Head of Professional Development
+49 (0)8092 7005-45
mmoosrainer@cadfem.de