Auslegung von Asynchronmaschinen mit Motor-CAD
Peter Dück
17.07.2024
Tech Artikel | 24/09
E-Maschinen sind allgegenwärtig, sobald es darum geht elektrische Energie in Bewegung und umgekehrt zu wandeln. Unter den vielen Arten von E-Maschine ist die Asynchronmaschine (ASM) eine der wichtigsten und verbreitetsten Maschinenarten. Daher ist die präzise Auslegung eine wichtige Aufgabe. Dies kann mit Ansys Motor-CAD multiphysikalisch realisiert werden kann.
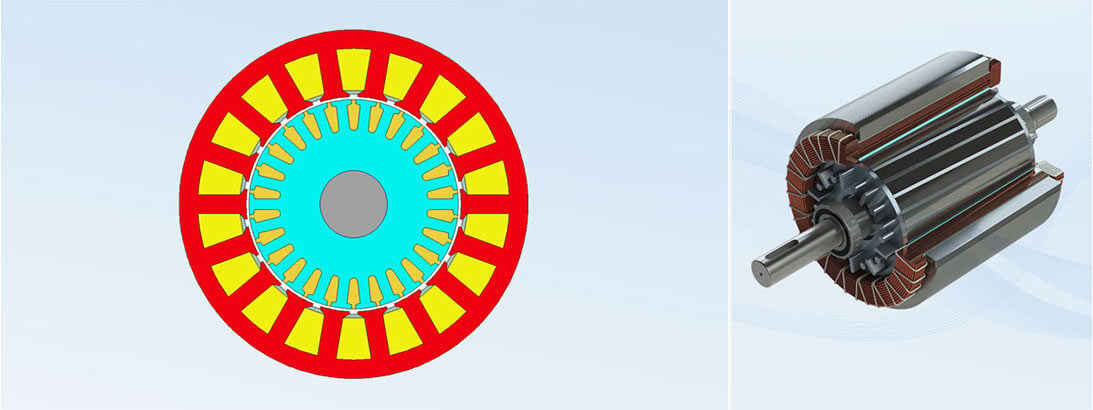
ASM vs. PMSM: Was ist eigentlich der Unterschied?
Es gibt zwei Maschinenarten, die sich für elektrische Maschinen durchgesetzt haben: Synchronmaschinen und Asynchronmaschinen, auch Induktionsmaschinen (IM) genannt. Unter den Synchronmaschinen ist die verbreitetste Variante die permanentmagneterregte Synchronmaschine (PMSM). Bei der PMSM dreht sich der Rotor synchron mit dem Drehfeld des Stators, bei der IM dreht sich der Rotor mit einer leicht anderen Drehzahl. Dieser Schlupf sorgt für grundlegend unterschiedliche Betriebseigenschaften. Während PMSM gut geeignet sind, um aus wenig Bauvolumen viel Leistung und Drehmoment herauszuholen und dabei in der Regel einen besseren Wirkungsgrad als IM haben, sind IM günstiger in der Fertigung und einfacher zu regeln.
Aufgrund der erwähnten Unterschiede ergeben sich leicht unterschiedliche Anwendungsgebiete. Synchronmaschinen werden in Kraftwerken und meistens auch in Windenergieanlagen als Generatoren verwendet. Weiterhin sind sie bei Servomotoren und in manchen Industrieantrieben im Einsatz. Induktionsmaschinen sind ebenfalls in zahlreichen Industrieantrieben vertreten. Sie werden weiterhin auch in Fahrantrieben, gerne auch als Linearantriebe eingesetzt. Beide Maschinenarten werden zudem momentan als Hauptantrieb in E-Fahrzeugen und elektrischen Bahnen verwendet.
Generatoren mit Turbinen für konventionelle Kraftwerke | © Adobe Stock
Besonderheiten bei der Auslegung in Motor-CAD
Die Induktionsmaschine ist also von Interesse, wenn man eine günstige, robuste und gut regelbare Maschine braucht und etwas Spielraum beim Bauraum hat. Aufgrund des Schlupfes bei IM erfolgt die Auslegung beider Maschinenarten unterschiedlich. PMSM lassen sich gut auch schon in einer frühen Designphase direkt mit 2D-FEM auslegen. Die Rechenzeit ist überschaubar, da ein eingeschwungener Zustand schnell erreicht werden kann. Bei IM sieht das jedoch anders aus. Diese Maschinenart lebt von den Wirbelströmen im Rotorkäfig, deren Berechnung sehr zeitaufwendig ist. Die Konsequenz ist, dass man IM zunächst analytisch auslegt und am Schluss numerisch die Ergebnisse verifiziert bzw. Optimierungen am Design durchführt.
Weiterhin gilt für elektrische Maschinen generell, dass sie eine Anwendung sind, die man prinzipbedingt nicht nur rein magnetisch betrachten kann. Mindestens die Drehmomentgleichung und damit das Einbringen einer Beziehung zwischen den elektrischen Klemmengrößen und den mechanischen Größen Drehmoment und Drehzahl ist notwendig für die Auslegung. Sobald diese Entwurfsphase einen bestimmten Reifegrad erreicht hat, stellen sich Fragen zu anderen physikalischen Domänen. Beispielsweise erwärmen sich elektrische Maschinen trotz eines Wirkungsgrades von oft über 90% deutlich. Eine aktive Kühlung durch Lüfter oder eine Flüssigkühlung sind keine Seltenheit.
Multiphysikalische Simulationen in Ansys Motor-CAD | © Ansys Inc.
Rotorfestigkeit – hält der Kurzschlusskäfig oder werden die Kurzschlussstäbe nach außen gerissen? – oder Akustik sind weitere Punkte, die ebenfalls berücksichtigt werden müssen. Ansys Motor-CAD liefert hier direkt in einem Tool die Möglichkeit, all diese Fragestellungen zu beantworten. Die kritischen Stellen bei der Thermik, Rotorfestigkeit und Akustik unterscheiden sich zwischen Synchronmaschinen und Asynchronmaschinen. Beispielsweise ist der Hotspot bei Synchronmaschinen üblicherweise in der Statorwicklung zu finden, bei Induktionsmaschinen ist das öfter mal der Käfigläufer. Dort verursachen hohe Wirbelströme eine deutliche Erwärmung des Käfigs, weshalb gelegentlich Kupfer als Käfigmaterial eingesetzt wird.
Das Ersatzschaltbild der Induktionsmaschine
Die analytische Berechnung der Induktionsmaschine ist nicht unbedingt ein Nachteil, weil analytische Berechnungen noch viel schneller sind als numerischen Simulationen. Die Herausforderung ist hier eher, die seit über 100 Jahren entwickelte sehr ausführliche Analytik der IM zu verstehen, damit man entsprechende Berechnungsprogramme überhaupt richtig nutzen und deren Ergebnisse interpretieren kann. Mit Ansys Motor-CAD haben wir ein hybrides Tool, welches die IM in vielerlei Hinsicht analytisch berechnen kann und für den Feinentwurf auch eine numerische Simulation anbietet.
Als analytischer Ansatz wird das sog. T-Ersatzschaltbild (T-ESB) verwendet: Ein elektrisches Netzwerk, welches mit zwei Maschen- und einer Knotengleichungen beschrieben werden kann. Wenn nun noch die Ersatzschaltbildelemente, die Widerstände und Induktivitäten variabel sind, können beliebige Arbeitspunkte berechnet werden. Die linke Seite des Ersatzschaltbilds repräsentiert den Stator mit seinem Ständerstrangwiderstand R1 und der Ständerstreuung X1. Die Ständerstreuung ist hier als Summe aller Streuanteile der Ständerseite zu verstehen. Sie enthält also u.a. die Ständernutstreuung und die Wicklungskopfstreuung. Die Hauptinduktivität (Xm) beschreibt die magnetische Kopplung zwischen Ständer- und Rotorfeld.
Ersatzschaltbild einer Induktionsmaschine | © CADFEM Germany GmbH
Da die Ständer- und Rotorwicklung galvanisch getrennt sind, müssten sich auch im ESB zwei Kreise ergeben. Zur Vereinfachung der Berechnung werden daher die Rotorgrößen auf den Ständer umgerechnet. Als Umrechnungsfaktor ü dienen dabei die Ständerwindungszahl w1 und die Rotornutzahl N2 jeweils bezogen auf das Grundfeld. Diese Werte werden als effektive Windungszahl interpretiert. Das Ganze ähnelt dadurch einer Getriebeübersetzung, nur eben elektrisch.
Mit diesem Faktor werden also die Rotorstreuung X2 und der Rotorwiderstand R2, hier auf zwei Teile gesplittet, multipliziert. Eine bereits enthaltene Erweiterung ist ein Widerstand zur Berücksichtigung der Eisenverluste RFe im ESB.
Betriebsverhalten im Einzellastpunkt
Eines der mit diesem ESB ermittelten Ergebnisse ist die Drehmoment-Drehzahl-Kennlinie, die sich bei Betrieb am starren Netz für unterschiedliche Belastungen ergibt. Hier sieht man schnell, welche Rotordrehzahl und damit welcher Schlupf zum höchsten Drehmoment führt. Im Synchronismus, also dem Fehlen einer Relativgeschwindigkeit zwischen dem Ständerfeld und dem Rotor, überträgt die Maschine kein Drehmoment, da keine Wirbelströme im Rotor induziert werden können, welche ein Rotorfeld aufbauen könnten, welches wiederum als Gegenpart einer Drehmomentbildung notwendig wäre. Damit liegt ein Leerlauf vor und die Kennlinie schneidet die X-Achse.
Drehmoment-Drehzahl-Kennlinie einer Asynchronmaschine | © CADFEM Germany GmbH
Früher, als man E-Maschinen vor allem für einen Arbeitspunkt, den sog. Bemessungspunkt, ausgelegt hat, hat man also versucht, das Design so zu wählen, dass bei der zu erwartenden Belastung der Maschine möglichst das Maximum des Wirkungsgrads der Maschine getroffen wird. Dieses Maximum befindet sich stets in der Nähe des oben dargestellten Maximums der Drehmoment-Drehzahl-Kennlinie, dem Kipppunkt. Die Maschine wird am Netz demnach zwischen dem Kipppunkt und dem Leerlaufpunkt betrieben. Der Großteil der Kennlinie beschreibt also instabiles Verhalten. Heute werden E-Maschinen jedoch zunehmend mehr bei unterschiedlichen Drehzahlen genutzt (E-Autos, Windkraftanlagen, Förderbänder…).
Wirkungsgrad und andere Größen im M-n-Kennfeld
Dafür benötigt man einen Umrichter. Mit ihm wird die Maschine immer im Maximum der Kennlinie betrieben, jedoch wird die Frequenz der Bestromung angepasst. Die Betrachtung eines ganzen Drehmoment-Drehzahl-Kennfelds (M-n-Kennfeld) wird möglich. Ansys Motor-CAD bietet hier Lösungen, um direkt die eigene Maschinenkonfiguration in ein Kennfeld „zu übersetzen“; und das nicht nur für IM und PMSM, sondern für alle gängigen Maschinentypen. Ein Vergleich zwischen IM und PMSM zeigt schnell, in welchen Bereichen welcher Maschinentyp überlegen ist. Stellt sich also die Frage, welcher Bereich im Kennfeld eigentlich für die Anwendung relevant ist.
Schematisches Wirkungsgradkennfeld einer IM (links) und einer PMSM (rechts) | © CADFEM Germany GmbH
In der linken Abbildung ist ein typisches Wirkungsgradkennfeld einer IM dargestellt, rechts sehen wir das Pendant für eine PMSM. Man erkennt, dass IM bei kleinen Drehzahlen eher zu schlechteren Wirkungsgraden neigen als PMSM. Dafür zieht sich ihr Wirkungsgradmaximum bis zur maximalen Drehzahl. Die Drehzahl, ab der die Maschine nicht mehr das maximale Drehmoment abgeben kann, nennt man Eckdrehzahl. Rechts davon beginnt der Feldschwächbereich. Da sich IM und PMSM hier grundsätzlich unterschiedlich verhalten, ergibt sich hier auch ein unterschiedlich starker Abfall der Grenzkennlinie. Bei PMSM fällt die Grenzkennlinie mit 1/n, also hyperbolisch mit der Drehzahl ab. Bei IM geht das schneller, nämlich mit 1⁄n2.
Kennfelder simulieren - Vollgas im Fahrzyklus!
Wir brauchen also Informationen zum Belastungsprofil oder zu einem Fahrzyklus, bei dem die Maschine z.B. einen möglichst hohen Wirkungsgrad erreichen soll. Für E-Autos ist der WLTP (Worldwide harmonized Light vehicles Test Procedure) Fahrzyklus ein guter Ansatz zur Auslegung eines Motors für ein E-Auto. Leitet man aus dem Geschwindigkeits-Zeit-Diagramm und einem angenommenen Fahrzeugmodell (cw-Wert, Masse…) die Drehmomentanforderung für bestimmte Drehzahlen ab, ergibt sich die dargestellte Punktewolke im M-n-Kennfeld. Damit ist klar, Ziel bei der Auslegung im variablen Betrieb ist, den Bereich des höchsten Wirkungsgrads so gut es geht so zu platzieren, dass die meisten Arbeitspunkte des Fahrzyklus darin liegen.
Um das zu erreichen, sind viele Iterationen mit einer schnellen Software notwendig. Wenn man dann noch die Physik versteht, die einem beispielsweise sagt, dass breitere Nuten im Stator zwar den Einbau von mehr Windungen in der Wicklung erlauben und damit das Statorfeld erhöhen können, aber gleichzeitig die Statorzähne schmaler werden, wodurch sie schneller in Sättigung gehen und dieser Effekt in einer größeren Ständerstreuung im Ersatzschaltbild erkennbar ist, dann kann man mit ein wenig Erfahrung schnell eine optimale Maschine simulieren. Im Kennfeld wirkt sich das wie folgt aus.
Wirkungsgradkennfeld einer IM mit unveränderten (links) und reduzierten Statorzähnen (rechts) | © CADFEM Germany GmbH
Ein Beispiel: Links ein Wirkungsgradkennfeld einer ASM mit originaler Geometrie, rechts mit 30% schmaleren Statorzähnen. Man erkennt, dass sich der Bereich hoher Wirkungsgrade hin zu betragsmäßig höheren Drehmomenten aufweitet. Dadurch verbessert sich der Wirkungsgrad einiger in blau eingezeichneter Arbeitspunkte des WLTP. Das klingt zunächst sehr positiv, allerdings verrät der in Motor-CAD ebenfalls bereitgestellte thermische Solver, dass sich das thermische Verhalten hierbei deutlich verschlechtert. Es zeigt sich: Um eine Asynchronmaschine unter Berücksichtigung aller Parameter fundiert auszulegen, ist ein multiphysikalischer Ansatz über Simulation unerlässlich – und Dank Motor-CAD zum Glück auch möglich.
Das Seminar zum Thema
-
Simulation von Induktionsmaschinen mit Ansys Motor-CAD
In diesem Seminar lernen Sie mehrere Simulationsansätze von Induktionsmaschinen anzuwenden.
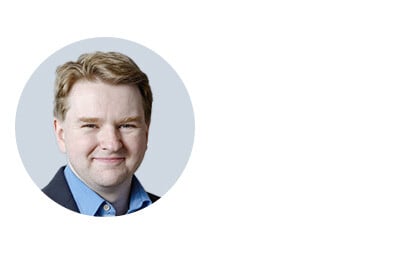
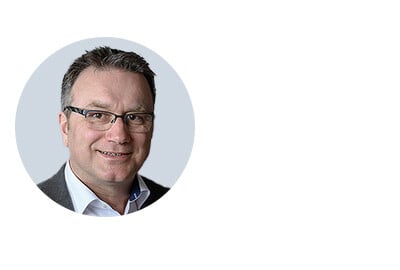
Redaktion
Dr.-Ing. Marold Moosrainer
Head of Professional Development
+49 (0)8092 7005-45
mmoosrainer@cadfem.de
Titelbilder: Links: © CADFEM GmbH | Rechts: © Adobe Stock
Zuerst veröffentlicht: Mai 2024