CO2 sparen mit Ansys Topologieoptimierung
Sebastian Hoffmann
15.07.2024
Tech Artikel | 23/06
Es wird ernst: CO2-Reduktion steht im Zentrum der Politik und ist für Gesellschaft wie Unternehmen überlebensnotwendig. Eine Minimierung der Bauteilmassen führt zu geringerem Energie- und Materialeinsatz in Herstellung und Betrieb und hilft so doppelt. In diesem Artikel zeigen wir anhand der Topologieoptimierung einer Triebwerkshalterung, wie Sie gezielt Masse einsparen können.
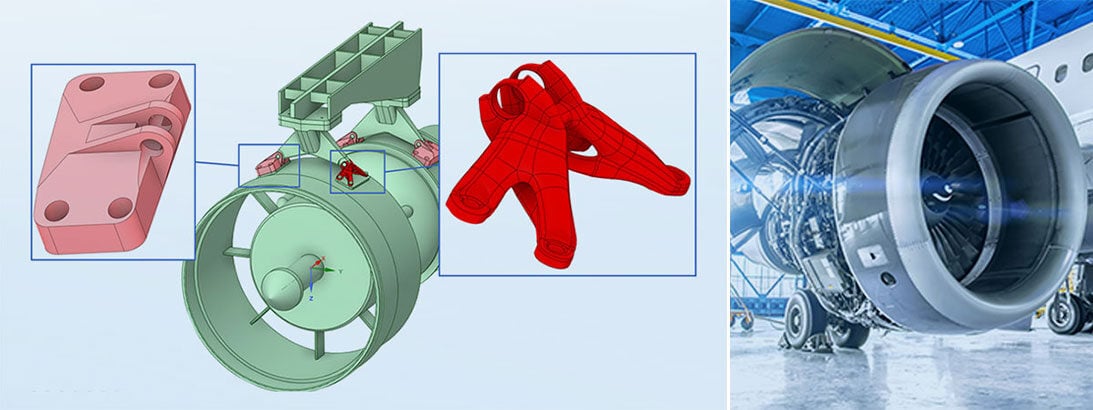
Ziel: weniger CO2 – Wie: Material sparen
Wir alle wissen, dass große Anstrengungen notwendig sind, um die CO2-Emissionen weltweit zu reduzieren. Doch welche Möglichkeiten dazu gibt es im Transportsektor? Aufgrund fehlender Alternativen und langer Entwicklungszyklen wird man insbesondere in der Luftfahrt auf absehbare Zeit nicht ohne fossile Brennstoffe auskommen können. Ein Weg CO2 einzusparen ist es, die Gesamtmasse zu reduzieren. Das wiederum bedeutet, dass jedes einzelne Bauteil gewichtsoptimiert werden muss. Eine verringerte Masse spart dabei doppelt: Bei der Herstellung wird weniger Material benötigt und im Betrieb wird weniger Treibstoff verbrannt.
Nicht jedem Bauteil sieht man sofort an, ob und vor allem wo überflüssiges Material eingespart werden kann. In Abhängigkeit der Belastung ergeben sich in jedem Bauteil Bereiche hoher und Bereiche niedriger Dehnungsenergie. Die stark belasteten Bereiche bilden die Lastpfade und sind wesentlich für die Funktion des Bauteils und müssen erhalten bleiben. Die Bereiche geringer Dehnungsenergie spielen aber keine Rolle und können weggelassen werden, um Gewicht zu sparen. Die große Preisfrage ist: Wie erkennt man die relevanten Bereiche? Ein guter Konstrukteur wird ein geeignetes Design mit Erfahrung und Bauchgefühl finden können. Ist der Entwurf aber wirklich optimal und was macht man als unerfahrener Ingenieur?
Egal ob ein bestehendes Bauteil optimiert oder vom weißen Blatt Papier begonnen werden soll: eine regelrechte Ideenmaschine für Jedermann stellt die Topologieptimierung dar. Hierbei nähert man sich iterativ einer optimalen Materialverteilung für das Bauteil. Dabei können z.B. eine geringe Masse, maximale Steifigkeit oder minimale Spannungen als Optimierungsziel definiert werden. Mit Nebenbedingungen kann die entstehende Form sogar hinsichtlich unterschiedlicher Fertigungsverfahren beeinflusst werden.
Flugzeugtriebwerk | © Adobe Stock
Topologieoptimierung – wie geht’s?
Die Topologieoptimierung ist nur eine der vielen Disziplinen der Strukturoptimierung (neben Form-, Topographie-, Lattice-Optimierung). Sie beruht darauf, dass ausgehend von einem vordefinierten Bauraum und einem maximal möglichen Ausgangsvolumen, nach und nach Material weggenommen bzw. entsprechend der Lastpfade umverteilt wird. Letztlich entsteht eine zusammenhängende Topologie. Bereiche, die erhalten bleiben sollen, wo Randbedingungen und Lasten eingeleitet werden, werden als Exklusion definiert und bei der Optimierung ausgeschlossen.
Wie definiert man, wo Material erhalten bleiben muss und gespart werden kann? Dazu existieren zwei Lösungsansätze in Ansys Mechanical: beim SIMP- (Solid Isotropic Material with Penalization-) Ansatz wird die sogenannte Pseudodichte als Parameter eingeführt. Jedes FE-Element erhält damit einen zusätzlichen Zustand, mehr oder weniger im Bauteil enthalten zu sein (rho = 0: kann weg, rho = 1: Material bleibt). Im Gegensatz dazu verzichtet die Level-Set-Methode auf einen Parameter. Die Oberfläche der Struktur wird durch eine Funktion beschrieben. Diese verändert sich ausgehend vom anfänglichen Bauraum hin zu einer optimalen Struktur. Es können sich mehrere nichtzusammenhängende Teilbereiche der Topologie ausbilden.
Wie bei jeder Optimierungsaufgabe bedarf es einer Zielfunktion, die das Optimierungsziel beschreibt. Eine Standardaufgabe ist die Maximierung der Steifigkeit einer Struktur. Dieser Punkt entspräche dem kleinsten Funktionswert der blauen Kurve. Er erfüllt aber nicht zwangsläufig die Kriterien einer real optimalen Struktur. Ein voll ausgefüllter Bauraum ist natürlich die steifste aller Lösungen aber keine Lösung der Aufgabenstellung. Dazu müssen zusätzliche Gleichheits- und Ungleichheitsbedingungen, sogenannte Restriktionen (rote Kurve), eingeführt werden. Beispielsweise könnte die Masse auf einen fixen Wert reduziert werden. Oder die Spannungen dürfen einen bestimmten Grenzwert nicht überschreiten.
Optimierungsproblem mit Nebenbedingungen und Optimierungsergebnis der Materialverteilung (entweder Pseudodichteverteilung oder Level-Set-Funktion) | © CADFEM Germany GmbH
Quick Reference Guide (QRG): Formulierung der Topologieoptimierungs-Aufgabe
Erhalten Sie mit dem QRG einen Auszug aus unserer Schulung "Lastgerechter Bauteilentwurf mit der Ansys Topologieoptimierung". Praxiswissen zum schnellen Nachschlagen im Arbeitsalltag, Formeln, Definitionen, Menübefehle und kurze Anleitungen kompakt für Sie aufbereitet. Sie interessieren sich für die gesamte Schulung zum Thema? Hier finden Sie alle Informationen!
QRG kostenlos downloaden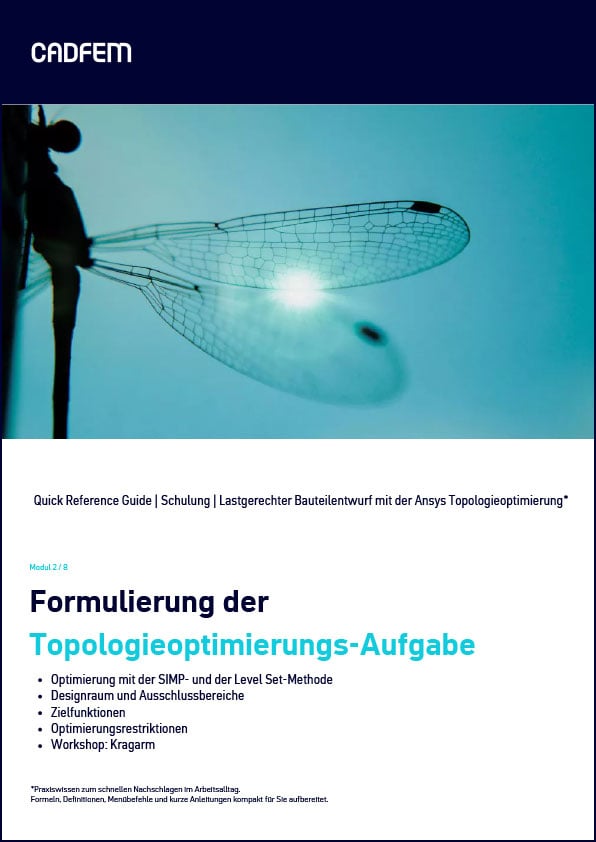
Und wie sieht es in der Software aus?
Voraussetzung für jede Topologieoptimierung ist eine vorangeschaltete Basis-Analyse (z.B. statische Analyse, Modalanalyse, thermische Analyse im System A). Die Geometrie der Basis-Analyse enthält das Bauteil mit dem maximal möglichen Bauraum. Es müssen sämtliche auftretenden Lasten und Randbedingungen enthalten sein. Denn das Optimierungsergebnis ist nur für diese definierten Lastszenarien optimal. Jede Änderung der Lasten und Randbedingungen oder jede fehlende Last kann zu veränderten Optimierungsergebnissen führen. Wie man es von anderen gekoppelten Systemen kennt, wird ein Structural Optimization-System mit der Basisanalyse verlinkt.
Unter dem Sammelbegriff Structural Optimization verbergen sich unterschiedliche Optimierungsansätze (dazu später mehr), u.a. die Topologieoptimierung mittels des SIMP-Ansatzes als Default. Lasteinleitungsstellen und Randbedingungen werden automatisch als Exklusionsbereiche definiert. Die Zielfunktion ist festzulegen, z.B. Minimierung der Masse, und die Restriktionen müssen definiert werden. Der Einfluss einzelner Lastschritte oder Eigenfrequenzen der Basisanalyse kann unterschiedlich stark gewichtet werden. Verformungs- und Spannungsergebnisse lassen sich direkt auf der optimierten Struktur darstellen. Diese Struktur liegt als STL-Körper vor und kann exportiert werden.
Um die Ergebnisse abzusichern, empfiehlt es sich im nächsten Schritt eine Validierungsrechnung basierend auf der rückgeführten CAD-Geometrie durchzuführen. Das Validierungs-System wird als Kopie des Basis-Systems angelegt. Die Ausgangsgeometrie wird jedoch durch die optimierte Geometrie ersetzt, die üblicherweise in Zelle C3 noch in eine CAD-Geometrie zurückgeführt wird. Verformungs- und Spannungsergebnisse des Validierungssystems können direkt mit der Basisanalyse verglichen werden.
Links: statische Basisanalyse, Mitte: Topologieoptimierung, rechts: Validierungsrechnung | © CADFEM Germany GmbH
reduzierte Masse
gegenüber dem Ausgangsbauraum
Beispiel: Bracket Flugzeugtriebwerk
Betrachten wir den konkreten Fall der Halterung eines Flugzeugtriebwerks: An vier Verschraubungspunkten ist das Bauteil fixiert. Gleichzeitig werden in mehreren Lastschritten der Basis-Analyse Kräfte und Momente auf die Bolzenlagerung aufgebracht. Als Material wird eine Aluminiumlegierung angenommen. Auch hier lautet die Zielfunktion: Maximierung der Steifigkeit. Die Masse soll auf 25 % des Ausgangsbauteils (maximaler Bauraum) reduziert werden. Die Abmessungen der sich möglicherweise einstellenden Streben (Member) werden durch einen Mindestwert von 15 mm begrenzt, so dass nicht zu filigrane Strukturen entstehen. Mögliche weitere Restriktionen können sein: Verschiebungen, Reaktionskräfte, globale Spannungen.
In diesem Fall wurde das Ziel einer gegenüber dem Ausgangsbauraum um 75 % reduzierten Masse erreicht. Das entspricht laut Ansys Granta Selector für die Legierung 6061 einer Einsparung von 16 kg CO2 je Bauteil – Einsparungen im Betrieb nicht eingerechnet. 16 kg CO2 klingt nicht viel, macht bei Stückzahlen von Tausenden oder gar Millionen aber den Unterschied. Zur Einordnung: Gegenüber einer erfahrungsbasiert konstruierten Halterung spart man sicher keine 75 %, aber vielleicht sind es 15 %, was immer noch eine ganze Menge ist. Und das Beste ist: diese Methode kann jeder anwenden, egal wie viele Halterungen er bereits in seinem Leben konstruiert hat!
Aber kann diese Struktur auch hergestellt werden und wenn ja, mit welchen Verfahren? Additive Fertigung würde sich hier anbieten, darüber hinaus wäre man aber in der Wahl des Herstellverfahrens eingeschränkt. Daher kommen jetzt die Fertigungsrestriktionen ins Spiel. Ist von vornherein bekannt, dass das Bauteil durch ein Gießverfahren hergestellt werden soll, lassen sich die Entformungsrichtungen der Gussform als Nebenbedingung definieren und es würde sich eine gießbare Struktur ausbilden. Darüber hinaus existieren weitere Fertigungsrestriktionen, die zum Beispiel zu einer strangpressbaren oder einer gehäuseähnlichen wasserdichten Struktur führen würden.
Ausgangsbauteil und Pseudo-Dichteverteilung der optimierten Struktur | © CADFEM Germany GmbH
Zurück zur CAD: Geometrierückführung
Das Optimierungsergebnis ist jedoch nur die halbe Miete. Die optimierte Struktur liegt als STL-Körper vor und kann als solche exportiert werden. Für die weitere Verwendung muss die Struktur aber idealerweise wieder in eine CAD-Geometrie überführt werden. Ansys Discovery liefert die notwendigen Werkzeuge dazu. Mittels Schrumpfverpacken (Shrinkwrap) lässt sich die tesselierte STL-Oberfläche mit einer glatteren Oberfläche überziehen. Entscheidend hierbei ist ein ausreichend klein, aber nicht zu klein gewählter Wert für die neu zu erzeugenden Dreiecksflächen.
Das anschließende Smoothing verfeinert die Oberfläche. Die Option „Flatten Peaks“ mit einem Grenzwinkel von 360° verrundet die Struktur so weit, dass damit die Auto-Skin-Funktion per Knopfdruck geschlossene Freiformflächen erzeugen kann und somit wieder eine CAD-Geometrie entsteht. Zuvor geschickt aus der Ausgangsgeometrie herausgeschnittene und wieder integrierte Bereiche können helfen, sauber konstruierte Flächen für Lasten und Randbedingungen zu generieren. Damit schließt sich der Kreis und wir können mit einem gewichtsoptimierten Bauteil im Entwicklungsprozess fortfahren.
Links: STL-Geometrie in Ansys SpaceClaim, Mitte: Ausgangsbauteil und optimiertes Bauteil im Vergleich, rechts: fertiges CAD-Guss-Bauteil | © CADFEM Germany GmbH
Das soll schon alles gewesen sein?
Wie schon erwähnt, ist die Topologieoptimierung nur ein Teil der Strukturoptimierung. Soll die Topologie der Struktur grundsätzlich unverändert bleiben, die Oberflächen jedoch optimiert werden, bieten sich die Optionen Formoptimierung für Volumenbauteile und Topographieoptimierung für Schalenstrukturen an. Hier werden mittels eines Mesh-Morphing-Algorithmus die Oberflächenknoten so verschoben, dass sich beispielsweise eine möglichst steife oder spannungsgünstige Oberfläche ergibt. Besonders steife Blechbauteile lassen sich durch optimal angeordnete Rippen und Sicken erzeugen.
Will man das äußere Erscheinungsbild eines Bauteils nicht grundlegend verändern, besteht die Möglichkeit im Innern eine Gitter- (Lattice-) Struktur statt Vollmaterial vorzusehen. Es kann aus einer Vielzahl unterschiedlicher Gittermuster gewählt werden. Die Durchmesser der Gitterstreben werden an die Belastungssituation angepasst. Im Bereich der Lastpfade werden entsprechend dickere Streben vorgesehen. Diese Strukturen sind dann nur noch additiv zu fertigen. Womit wir zum nächsten Schritt im Produktentwicklungsprozess kommen.
Selbstverständlich kann auch der Herstellprozess eines additiv gefertigten Metall-Bauteils simuliert werden. Dabei spielt es keine Rolle, ob ein Pulverbett-, DED- oder Sinter-Verfahren zum Einsatz kommt. Die Software hilft, kritische Bereiche schon vor dem Druck zu identifizieren. Zudem liefert die Verzugskompensierung ein derart vorverformtes Bauteil, dass beim Druck ein annähernd verzugsfreies Endergebnis erreicht werden kann. Die Simulation hilft so teure Fehldrucke zu vermeiden. Die Kombination aus Strukturoptimierung und Prozesssimulation bringt so innovative und effiziente Bauteile hervor. Probieren Sie es selbst, beschreiten Sie neue Wege im Designprozess!
Links: Topographieoptimierung, Mitte: Lattice-Optimierung, rechts: Simulation des 3D-Druckprozesses | © Ansys Inc.
Seminare zum Thema
-
Lastgerechter Bauteilentwurf mit der Ansys Topologieoptimierung
Lernen Sie, automatisch eine optimale Materialverteilung in einem gegebenen Bauraum unter strukturmechanischen Belastungen zu erzeugen und validieren.
-
Systematische Werkstoffauswahl mit Ansys Granta Selector
Lernen Sie, wie Sie Werkstoffeigenschaften aus den Produktanforderungen ableiten und geeignete Werkstoffe strukturiert und sicher finden.
-
Additive Fertigungsprozesse im Metalldruck simulieren
In diesem Seminar lernen Sie, mit Ansys Mechanical den 3D-Druckprozess für Bauteile zu simulieren, um Geometrie, Bauteilorientierung & Verzug zu optimieren.
-
Intensiv-Workshop: Strukturmechanik
Ein Must-Have für alle Strukturmechaniker: Nach diesem Workshop schauen Sie Ihre Modelle mit anderen Augen an - garantiert.
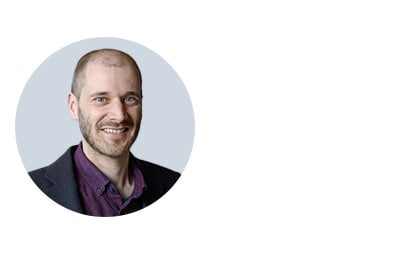
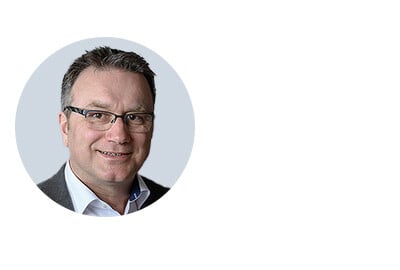
Redaktion
Dr.-Ing. Marold Moosrainer
Head of Professional Development
+49 (0)8092 7005-45
mmoosrainer@cadfem.de
Titelbilder: Links: © CADFEM Germany GmbH | Rechts: © Adobe Stock
Zuerst verüffentlicht: Oktober 2023