Schraube locker? Schnelle Auslegung mit Discovery!
Özcan Özcicek
16.07.2024
Tech Artikel | 24/01
Sie sind praktisch, flexibel, wirtschaftlich in der Umsetzung und jeder kennt sie: Schrauben. In diesem Artikel wollen wir an einem Maschinengehäuse einen Workflow zur Schraubenvorauslegung aufzeigen. Das Ziel dabei ist, die Anzahl der benötigten Schrauben, aufgrund von Platzmangel und zu hohem Montageaufwand, von ursprünglich 28 auf höchstens 12 zu reduzieren.

Typischerweise sind in der frühen Entwicklungsphase viele Informationen wie beispielsweise exakte Belastungswerte, genaue Materialwerte oder die Produktionsverfahren noch nicht vollständig definiert. Sehr häufig passiert es auch, dass sich die Anforderungen im Laufe der weiteren Entwicklungsphasen, zum Beispiel aufgrund von Kundenwünschen, ändern.
Dabei ist die Gestaltung der Schraubenverbindung nicht nur eine Frage der Festigkeit. Sie hat neben dem Produktdesign auch weitreichende Auswirkungen auf eine Reihe von Aspekten für den gesamten Produktlebenszyklus. Dazu gehören z.B. die strukturelle Performance der Verbindungsstelle, Montage-, Reparatur- und Wartungsaufwände oder Risiken von Materialbrüchen, unerwünschte Lockerungen und Energieverlusten durch Vibrationen.
Deshalb ist die Möglichkeit sehr wertvoll, bereits in einem frühen Produktentwicklungsstadium schnell, einfach und mit wenigen Eingaben eine Vorabschätzung der Anzahl, der Größe oder der Position der benötigten Schrauben durchzuführen. Dabei reden wir bewusst von einer „Vorauslegung“ und nicht von einem „Nachweis“. Der Fokus liegt auf einer qualitativen Aussage, die selbst von nicht Berechnungsspezialisten schnell durchgeführt werden kann.
Gehäuseverschraubung in Ansys Discovery | © CADFEM Germany GmbH
Schraubensimulation, ist das nicht aufwändig?
Wenn es um die Dimensionierung der Schrauben geht, ist das Anpassen der Geometrie in den meisten Fällen mit überschaubarem Aufwand realisierbar. Die Schraubenberechnung kann aber schon mit umfangreichem Aufwand verbunden sein. Viele CAD-Systeme stellen die Schrauben in Bibliotheken zur Verfügung, oft viel zu detailliert, mit Gewinde, Außensechskant und sogar der Unterlegscheibe. Für die klassische FEM-Simulation kann dies bereits eine große Hürde darstellen. Um das Modell mit akzeptablem Aufwand simulieren zu können, ist ein gründliches Defeaturing notwendig. Wenn anschließend noch die Themen Materialdefinition und Vernetzung folgen, fällt dieser Workflow rasch aus der Rubrik „schnell und einfach“ heraus.
Ansys Discovery hat die Funktion „Assign Bolts“ implementiert. Mit „Assign Bolts“ werden Schrauben sowie die zugehörigen Bohrungen auf Knopfdruck automatisch identifiziert. Das System bietet anhand des Durchmessers und der Bohrungstiefe geeignete Schraubengrößen nach den Standards von Eurocode, SAE und ASTM an. Die Schrauben werden nach Größe und Festigkeitsklasse aufgelistet. Dies erspart dem Anwender aufwändiges Geometrieaufbereiten und suchen nach passenden Material - und Schraubendaten in Tabellen.
Mit dem Bestätigen der ausgewählten Schraubengröße werden automatisch die Verbindungselemente für die Simulation erstellt. Darin sind sowohl die geometrischen Schrauben, die als Balken (Modellklasse 2) diskretisiert werden, auch die Materialgrenzwerte je nach spezifischer Schraubengröße hinterlegt. Nach der Durchführung der Simulation werden alle Schrauben in einem automatisierten Prozess ausgewertet. Für eine schnelle Übersicht erhält man für jede Schraube, basierend auf den Sicherheitsfaktor für die Zugfestigkeit und die Scherfestigkeit, eine farbliche Darstellung. Die exakten Werte der Sicherheitsfaktoren kann man ebenfalls je Schraube darstellen oder als gesamte Tabelle exportieren.
Datenbank mit Schraubengrößen und Materialeigenschaften in Ansys Discovery | © CADFEM Germany GmbH
Schrauben und Kontakte – ein Angstthema? Nein!
Erfahrungsgemäß kommt eine Schraube selten allein. Meistens sind es mehrere, manchmal mehrere hunderte. Entsprechend ist der zeitliche Aufwand für die Definition der Kontakte für das Simulationsmodell nicht ganz unerheblich. Die Kontakte am Schraubenkopf, am Schaft der Schraube und am Gewinde müssen sowohl erstellt als auch eingestellt werden, in ungünstigsten Fällen sogar für jede einzelne Schraube. Der hier vorgestellte Workflow in Ansys Discovery mit der Funktion „Assign Bolts“ adressiert auch diesen Punkt und übernimmt die Aufgabe der Kontaktdefinitionen der Schrauben vollständig.
Der Kontakt zwischen Schraubenkopf und Flansch sowie der zwischen Gewinde und Bohrung wird automatisch mit MPC-Verbundkontakten abgebildet. Dies setzt also voraus, dass der Schraubenkopf bei Belastung keine Gleitbewegung vollziehen kann. Ebenfalls wird ein Loslösen des Gewindes damit unterdrückt . Die Gehäusehälften können mit einem reibungsbehafteten Kontakt miteinander verbunden werden. Dieses sind gängige Annahmen für einfache Betrachtungen. Wie oben bereits erwähnt, geht es in diesem Workflow um eine Vorauslegung und nicht um eine Nachweisführung. Mit diesen Kontakteinstellungen ist eine schnelle und robuste Simulation ohne Vernetzungs- und Konvergenzherausforderungen für die meisten Aufgaben sichergestellt.
Mit der Funktion "Schrauben zuweisen" in Ansys Discovery definierte Schrauben | © CADFEM Germany GmbH
Schrauben neu dimensionieren - Schritt für Schritt
In diesem repräsentativen Beispiel werden eine Überprüfung und Dimensionierung einer Gehäuseverschraubung durchgeführt. Anfänglich sind für das Modell bei den vorgeschriebenen Belastungen 28 Schrauben M5 mit der Festigkeitsklasse 4.6 vorgesehen. Auf jeder Seite befinden sich 8 Schrauben mit gemeinsamen Eckschrauben. Die Aufgabe besteht darin, aufgrund enger Montageverhältnisse, die Anzahl der Schrauben zu verringern. Es dürfen je Seite maximal 4 Schrauben eingesetzt werden. Dabei ist sicherzustellen, dass eine zuverlässige und sichere Verbindung gewährleistet ist. Die Schraubengröße soll M8 nicht überschreiten. Alle Schrauben werden mit den jeweils zulässigen Schraubenvorspannkräften aus DIN 912 vorgespannt.
Bei dem Betrachteten Modell handelt es sich um zwei Maschinengehäusehälften aus Stahl. Das untere Segment wird im inneren mit Öldruck beansprucht. Auf dem oberen Segment befinden sich weitere Aufbauten. Die Belastung dieser Aufbauten durch ihr Eigengewicht wird mit einer Punktmasse im Schwerpunkt auf die obere Verbindungsfläche mit der Erdbeschleunigung aufgebracht. Die Simulation stellt den Betriebslastfall im Worst-Case-Szenario dar.
Bei der Auswertung des Ausgangsmodells in Discovery ergibt sich ein minimaler Sicherheitsfaktor für die Zugfestigkeit von 1.14. Somit ist eine ausreichende Sicherheit bei der betrachteten Belastung gegeben. Jedoch ist der Sicherheitsfaktor nur knapp größer 1. Es ist zu vermuten, dass durch eine Reduzierung der Schraubenanzahl der Sicherheitsfaktor unter 1 sinken wird. Wir möchten eine systematische Überprüfung der Schraubengrößen bei 4 Schrauben je Seite durchführen. Obwohl wir aus den Ergebnissen des Ausgangszustandes vermuten können, dass die Schraubengröße M5-4.6 nicht ausreichen wird, wollen wir uns an die benötigte Mindestschraubengröße von unten antasten.
Ausgangsmodell mit 28 x M5-4.6: Knapp, aber aufgrund der zu hohen Schraubenanzahl alles im grünen Bereich | © CADFEM Germany GmbH
Weniger Schrauben, mehr Platz
Wenn das Geometriemodell parametrisch aufgebaut ist, beispielsweise mit der HistoryTracking Funktion in Discovery, oder aber auch in einem externen CAD-System, kann die Schraubengröße und -anzahl auf eine schnelle Weise angepasst werden. Das vorliegende Modell der Gehäuseverschraubung ist vollständig im Discovery parametrisiert und daher sehr schnell anpassbar.
Das Ergebnis der Schraubenauswertung der angepassten Variante mit 4 Schrauben M5-4.6 je Seite zeigt, dass der Sicherheitsfaktor für die Zugfestigkeit bei 5 von 12 Schrauben deutlich unter 1 fällt. Bei den restlichen Schrauben liegt dieser Wert zwischen 0.91 und 1.08 und somit ebenfalls im Grenzbereich. Für die nächste Variante wird die größere Schraubendimension M6-4.6 erstellt.
Auch nachdem die Schraubengröße im Geometriemodell auf M6-4.6 aktualisiert wurde, ergibt sich in der Auswertung bei einer Schraube ein Sicherheitsfaktor für die Zugfestigkeit von 0.805 und somit immer noch deutlich < 1. Bei weiteren 3 Schrauben liegt dieser Wert weiterhin im Grenzbereich zwischen 0.91 und 1.07.
Fast alle Schrauben fallen bei 12 x M5-4.6 durch | © CADFEM Germany GmbH
Besser, aber 12 x M6-4.6 sind noch nicht gut genug | © CADFEM Germany GmbH
Besser nicht zu knapp auslegen
Bei der nächstgrößeren Schraubendimension M8 – 4.6 liegt der Sicherheitsfaktor der Zugfestigkeit zwischen 1.0 und 1.77 und somit bei keiner Schraube unter 1. Jedoch ist eine Schraube im Grenzbereich. Mit der Verwendung von M8er Schrauben ist die definierte größtmöglich zulässige Schraubengröße für diese Aufgabe erreicht. Eine zusätzliche Erhöhung der Sicherheitsfaktoren kann durch Anpassen der Festigkeitsklasse beispielsweise von 4.6 auf 5.6 erreicht werden.
Die Änderung der Festigkeitsklasse geschieht auf Knopfdruck in der Funktion „Assign Bolts“. Da es sich um keine geometrische Änderung handelt, muss die Simulation nicht zwangsläufig neu durchgeführt werden, es sei denn die Schraubenvorspannkraft ändert sich. Das ist in unserem Modell jedoch nicht der Fall. Eine Aktualisierung der Schraubenauswertung ist ausreichend. Der Sicherheitsfaktor der Zugfestigkeit erhöht sich und liegt nun mit einem komfortablen Puffer zwischen 1.25 und 1.86.
Die Erkenntnis in diesem Beispiel ist nicht nur begrenzt auf die Zahlenwerte der Sicherheitsfaktoren. Genauso wertvoll ist der Know-how-Gewinn. Der Anwender erfährt und versteht schnell die Zusammenhänge, in welchen Bereichen die Schrauben höher belastet sind als in anderen Bereichen und welche zusätzliche Sicherheit eine Änderung der Schraubengröße oder der Anzahl bewirken kann. Des Weiteren könnte man mit diesem Workflow auch eine ungleichmäßige Anordnung der Schrauben untersuchen. Bis hin zur gezielten Positionierung der Schrauben, da wo sie benötigt werden. Eine Optimierung der Schraubenpositionen, das wäre ein schönes Thema für einen weiteren Artikel …
Fast am Ziel mit 12 x M8-4.6 | © CADFEM Germany GmbH
Optimierte Vorauslegung mit 12 x M8-5.6 | © CADFEM Germany GmbH
Next step: Bewertung nach spezifischen Richtlinien
Ansys Discovery nutzt den Vorteil der integrierten Eurocode 3 Datenbank in Kombination mit den leistungsfähigen Modellierungsfunktionen und den bewährten Ansys Solvern. Durch die Implementierung in der Funktion „Assign Bolts“ ist die Vorauslegung mit dieser Methode für jeden Ingenieur schnell realisierbar. Wenn es später im Entwicklungsprozess an den Nachweis von Schraubenverbindungen geht, gibt es mit Eurocode 3 und VDI 2230 zwei verschiedene Richtlinien, die sich mit diesem Thema befassen.
Eurocode 3 ist eine europäische Richtlinie für den Stahlbau, während VDI 2230 „Systematische Berechnung hochbeanspruchter Schraubenverbindungen“ eine Richtlinie des Vereins Deutscher Ingenieure (VDI) ist, die sich mit der Berechnung von Schraubenverbindungen im Maschinenbau befasst. Eurocode 3 bietet eine umfassende Abdeckung für verschiedene Anwendungen im Stahlbau. Der Vorteil dieser Richtlinie ist, dass wenig Informationen benötigt werden, um eine Aussage treffen zu können. Bei der VDI 2230 ist das deutlich anders. Sie ist speziell auf Schraubenverbindungen im Maschinenbau ausgerichtet und insgesamt sehr viel detaillierter.
Trifft dieses Thema bei Ihnen einen Nerv? Dann werfen Sie einen Blick auf die unten verlinkten Seminare. Die Bandbreite geht von der Vorauslegung mit Discovery bis zur Nachweisführung in Mechanical mit dem Tool „Bolt Assessment inside ANSYS“. Und wenn Sie sich nicht sicher sind, was für Ihre Aufgaben die besser geeignete ist, dann sprechen Sie uns gerne an. Wir werden gemeinsam eine Lösung finden.
Seminare zum Thema
-
Ansys Discovery Update-Seminar für Strukturmechanik
Lernen Sie mehr über neue Funktionalitäten in Ansys Discovery mit Fokus auf vorausgewählte Themen der aktuellen Versionen.
-
Simulation von Schraubenverbindungen nach VDI 2230
Lernen Sie, den systematischen Festigkeitsnachweis nach VDI-Richtlinie 2230 korrekt und direkt in Ihrer Simulation durchzuführen.
-
Intensiv-Workshop: Strukturmechanik
Ein Must-Have für alle Strukturmechaniker: Nach diesem Workshop schauen Sie Ihre Modelle mit anderen Augen an - garantiert.

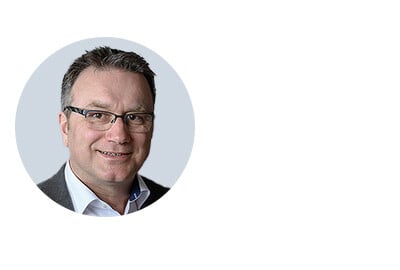
Redaktion
Dr.-Ing. Marold Moosrainer
Head of Professional Development
+49 (0)8092 7005-45
mmoosrainer@cadfem.de
Titelbilder: Links: © CADFEM Germany GmbH | Rechts: © Adobe Stock
Zuerst veröffentlicht: Januar 2024