Wasserstoff statt Erdgas: Optimale Brennergeometrie durch CFD-Simulation
Dr.-Ing. Fabian Findeisen
16.07.2024
Tech Artikel | 23/09
Sie haben einen Industriebrenner, der mit Erdgas betrieben wird, und wollen auf Wasserstoff umsteigen? Das klingt nach einer guten Idee, denn Wasserstoff ist ein sauberer und erneuerbarer Energieträger, der die CO2-Emissionen reduzieren kann. Aber können Sie einfach den gleichen Brenner verwenden? Und wie können Sie das herausfinden, ohne viel Geld und Zeit zu investieren? Erfahren Sie in diesemArtikel mehr über die Möglichkeiten der CFD-Simulation und lassen Sie sich inspirieren durch praktische Tipps zur Gittergenerierung, den Verbrennungsmodellen und dem neuen GPU-Solver.
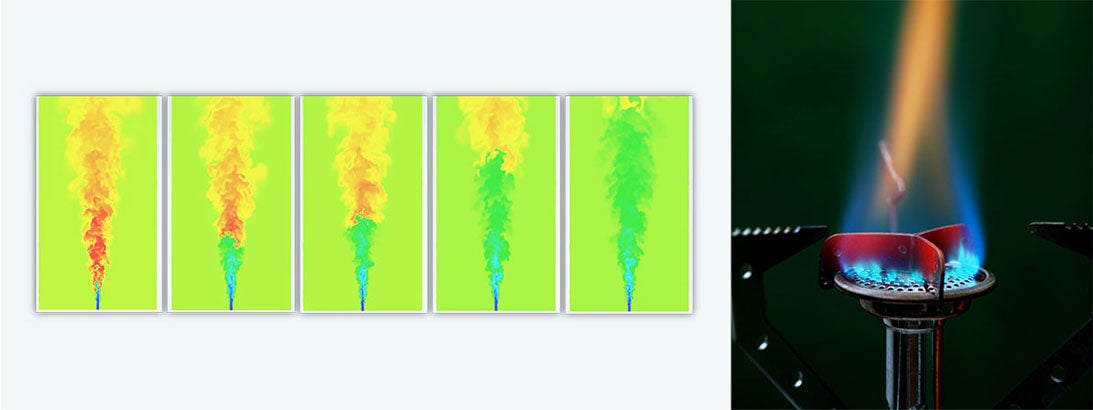
Warum sollte ich die Verbrennung simulieren?
Wasserstoff hat andere physikalische und chemische Eigenschaften als Erdgas. Dadurch verhält sich die Verbrennung von Wasserstoff auch anders als die von Erdgas. Zum Beispiel hat Wasserstoff eine höhere Flammengeschwindigkeit, eine niedrigere Zündtemperatur und eine höhere Reaktivität. Das hat Auswirkungen auf Stabilität, Effizienz und Emissionen der Flamme. Wenn Sie also einfach den gleichen Brenner verwenden, der eigentlich für Erdgas ausgelegt ist, könnten Sie nicht die gewünschte Leistung erzielen oder sogar Sicherheitsprobleme bekommen.
Zum Beispiel kann es zu einem Flammenrückschlag (sog. Flashback) oder einer unvollständigen Verbrennung kommen. Das kann zu einem erhöhten Verbrauch von Wasserstoff, einer verringerten Wärmeübertragung oder einer erhöhten Bildung von Stickoxiden (NOx) führen. Um das zu vermeiden, ist es empfehlenswert den Brenner für Wasserstoff anzupassen. Dazu gehören die Änderung des Brennstoff-Luft-Verhältnisses, des Drucks, der Temperatur oder auch der Geometrie des Brenners. Vielleicht wollen Sie auch untersuchen, wie sich verschiedene Mischungsverhältnisse aus Erdgas und Wasserstoff verhalten? Aber wie finden Sie heraus, welche Parameter Sie ändern müssen?
Das ist nicht so einfach zu beantworten, denn die Verbrennung von Wasserstoff ist ein komplexer Prozess, der von vielen Faktoren abhängt. Mit einem leistungsstarken Simulationswerkzeug können Sie die Strömung, die Verbrennung und die Wärmeübertragung in Ihrem Brenner virtuell modellieren und verschiedene Szenarien testen. So können Sie die optimale Konfiguration für Ihren Brenner finden, bevor Sie ihn in der Realität einsetzen.
Die Verbrennung von Wasserstoff zeigt einige Besonderheiten, die beim Umstieg von Erdgas auf Wasserstoff beachtet werden sollten | © CADFEM Germany
Wie kann mir die CFD-Simulation helfen?
Hier kommt Ansys Fluent für die CFD-Simulation ins Spiel. CFD steht für Computational Fluid Dynamics und ist eine Methode, um die Strömung von Gasen und Flüssigkeiten numerisch zu berechnen. Mit CFD-Simulationen können Sie Ihren Brenner virtuell nachbilden und verschiedene Parameter variieren. So können Sie sehen, wie sich die Strömung, die Verbrennung und die Wärmeübertragung in Ihrem Brenner verhalten und welche Auswirkungen das auf die Leistung und die Emissionen hat. Sie können auch verschiedene Brennerdesigns vergleichen und das beste auswählen.
Weitere Vorteile der CFD-Simulation von Industriebrennern sind:
- Geld und Zeit sparen: Keine realen Tests mit teuren Prototypen notwendig.
- Sicherheit erhöhen: Flammenrückschlag und Selbstentzündung vorhersagen und vermeiden.
- Effizienz und Umweltverträglichkeit verbessern: Brennstoff-Luft-Verhältnis optimieren und NOx-Emissionen reduzieren.
Auf dem Weg zum virtuellen Prototyp muss die Geometrie definiert, das Rechengitter erstellt und das Verbrennungsmodell ausgewählt werden | © CADFEM Germany
Verbrennung simulieren – Mit dem Gitter starten
Haben Sie die ersten Schritte gemeistert und ihre Aufgabenstellung klar umrissen, lohnt es sich das Augenmerk auf die Gittergenerierung zu richten. Das aus einzelnen Zellen bestehende Gitter beeinflusst maßgeblich die Genauigkeit und Stabilität der Simulation. Ein qualitativ hochwertiges Gitter sollte immer folgende Eigenschaften aufweisen:
- Ausreichende Auflösung zur Erfassung aller relevanten Strömungsstrukturen,
- glatter Übergang zwischen Regionen, um den numerischen Fehler zu verringern, und
- eine möglichst orthogonale Ausrichtung der Zellflächen zu den Stromlinien.
Wie sieht nun ein geeignetes Gitter für die Wasserstoffverbrennung aus? Hier ein paar Tipps für die optimale Gittergenerierung [1]. Die Tabelle unten liefert eine Orientierung wichtiger Netzeinstellungen für den Brenner selbst samt Düsen für das Einströmen der Reaktanden, für die Brennkammer und deren Kern sowie für die Außenbereiche, in denen keine Reaktion stattfindet. Im Detail erfordert jede CFD-Simulation natürlich immer eine Sensitivitätsstudie um den Einfluss der Gitterauflösung zu minimieren. Sollen turbulente Strukturen der Strömung und die Interaktion aus Chemie und Strömung besonders detailliert berechnet werden, kann aber auch eine deutlich feinere Vernetzung erforderlich sein.
Übrigens: Mit der in Ansys Fluent patentierten MOSAIC Poly Hexcore Technologie erhalten Sie ein hochwertiges strukturiertes Gitter in der Brennkammer, welches sich exzellent auch auf einem Cluster berechnen lässt. Und mit dem Fault-Tolerant Meshing Workflow können Sie auch schwierige und komplizierte CAD-Geometrien vernetzen, da die Methode automatische Korrekturmechanismen bereitstellt. Sollten Sie sich mit benötigten Netzauflösung doch nicht sicher sein oder wollen sie nur die Flammenfront genauer auflösen, können Sie die adaptive Vernetzung für Polyeder-Netze nutzen (PUMA-Algorithmus). Ein vordefiniertes Kriterium basierend auf dem sog. Flame Indicator verfeinert das Gitter nur da, wo es gerade nötig ist [2].
1. Brenner und Brennkammer |
Ein Body of Influence (BOI) im Brenner verfeinert das Netz, sodass mindestens 20-25 Zellen über dem Durchmesser existieren. Am besten den BOI mit dem 3-4-fachen des Brennerdurchmessers in die Brennkammer verlängern. |
|||||
2. Brennkammerkern |
Der BOI sorgt für ein hochwertiges und gleichmäßiges Gitter im Kern und verbessert so die Auflösung von Mischung, Flammenfront und Emissionen. |
|||||
3. Einströmdüsen des Brenners |
8-10 Zellen über dem Lochdurchmesser reichen, um ein Auslöschen der Flamme vorherzusagen. |
|||||
4. Außenbereiche |
Die Auflösung außerhalb des Kerns kann gröber sein, idealerweise etwa doppelt so groß wie im Kern. |
Für die Erstellung eines Gitters im Inneren eines Wasserstoffbrenners kann der Brennraum in verschiedene Bereiche unterteilt werden.
Mit dem Poly-Hexcore Meshing in Ansys Fluent erzeugen Sie das für Ihre Brennergeometrie passende Gitter. Die einzelnen Bereiche im Inneren (1-4) sind in der Tabelle erklärt | © Ansys, CADFEM Germany GmbH
Quick Reference Guide (QRG): Vernetzung für Außenströmungen und Gitterqualität
Erhalten Sie mit dem QRG einen Auszug aus unserer Schulung "Praxisgerechtes Vernetzen mit Ansys Fluent Meshing". Praxiswissen zum schnellen Nachschlagen im Arbeitsalltag, Formeln, Definitionen, Menübefehle und kurze Anleitungen kompakt für Sie aufbereitet. Sie interessieren sich für die gesamte Schulung zum Thema? Hier finden Sie alle Informationen!
QRG kostenlos downloaden
Welches Verbrennungsmodell ist das passende? EDC vs. FGM-Modell
Kommen wir nun zur Wahl des passenden Verbrennungsmodells. Dies sollte so gewählt werden, dass es die chemischen Reaktionen und die Turbulenz-Chemie-Wechselwirkungen ausreichend genau beschreibt. Verbreitete Modelle sind das EDC (Eddy Dissipation Concept) und das FGM (Flamelet Generated Manifold). Das EDC-Modell basiert auf der Idee, dass chemische Reaktionen in den feinsten turbulenten Wirbeln stattfinden. Die Reaktionsrate wird durch die Wirbelgröße und -frequenz beeinflusst, die wiederum von der Turbulenz abhängen. Konkret nutzt das EDC-Modell einen umfangreichen Reaktionsmechanismus und löst die Reaktionsgleichungen mithilfe effizienter Tabellierungs-Algorithmen wie dem ISAT (In-Situ Adaptive Tabulation Algorithmus).
Im Gegensatz dazu basiert das FGM-Modell auf der Annahme, dass die innere Flammenstruktur einer eindimensionalen Darstellung folgt. Diese wird vorab mithilfe eines laminaren 1D-Flammenlösers wie Chemkin berechnet und tabelliert. Das FGM-Modell kann zum Beispiel mit dem Skeletal Reaktionsmechanismus kombiniert werden, welcher 10 Gaskomponenten (die sog. Species) sowie 25 Reaktionen enthält. Reicht der Reaktionsumfang nicht aus, ist der UCSD-Mechanismus (57 Species, 268 Reaktionen) eine Alternative. Die folgende Tabelle vergleicht EDC und FGM-Modell. Die Tabelle darunter liefert ein Beispielsetup zum FGM-Modell für eine teilweise vorgemischte Flamme, ebenso wie Empfehlungen zu numerischen Einstellungen. Genügend große Durchflusszeiten gewährleisten eine aussagekräftige transiente Mittelung der Resultate.
Wenn wir über Verbrennung sprechen, müssen wir auch das Turbulenzmodell beachten. Für Fälle mit stabilen Strömungsfeldern, stellen RANS-Modelle (k-ω SST, Realizable k-ϵ) eine effiziente Lösung für viele Ingenieurprobleme dar. Oft liegt aber eine starke Kopplung zwischen Strömung und Reaktion vor. So führen instabile Strömungen bspw. zur lokalen Auslöschung der Flamme. Um Flammenbildung und Schadstoffemissionen möglichst genau zu erfassen, ist eine Large Eddy Simulation (LES) die beste Wahl. LES gilt im Allgemeinen jedoch als sehr aufwendig. Ein guter Kompromiss zwischen Genauigkeit und Aufwand stellt die Stress-Blended Eddy Simulation (SBES)dar, weil sie zwischen RANS und LES-Modell umschalten kann.
Die Verbrennungsmodelle EDC und FGM im Vergleich
Combustion Model |
Advantages |
Disadvantages |
|||||
|
|
|
|||||
Flamelet Generated Manifold (FGM) |
Advantageous for applications with fast reactions or partial premixing, such as gas turbines or process furnaces, due to low calculation times. |
May have difficultly capturing flashback or detonations. |
Beispielsetup: Wasserstoffverbrennung mit dem FGM-Modell für eine partiell vorgemischte Flamme
Turbulenz |
Verbrennung |
Reaktions-mechanismus H2 |
Durchflusszeiten |
|||||
|
|
|
|
|||||
Diskretisierung |
p-u-Kopplung |
Zeitschritt & Sub-Iterationen |
||||||
Other: |
|
|
|
Und nun? Simulieren mit dem GPU Solver in Ansys Fluent
Detaillierte und komplexe Methoden wie EDC und LES erfordern große Rechenkapazitäten. Doch was tun, wenn kein High Performance Cluster zur Verfügung steht? Der neue GPU Solver in Ansys Fluent bietet hier die Lösung, da die Berechnung vollständig auf einer oder mehrerer Grafikkarten ausgeführt werden kann. Dies ermöglicht eine Beschleunigung der Rechenzeit um ein Vielfaches im Vergleich zu herkömmlichen CPU-Lösern, was nicht nur zu Zeitersparnis, sondern auch zu erheblichen Energieeinsparungen führt. Mit einer wachsenden Modellvielfalt im GPU-Solver sind Ingenieure so in der Lage, komplexe Berechnungen in Rekordzeit durchzuführen, was neben präzisen Ergebnissen auch umfassende Variantenstudien ermöglicht.
Neben Verbrennungs- und Turbulenzmodell können natürlich noch weitere physikalische Aspekte ergänzt werden: So spielt Strahlung und deren Wirkung auf die Reaktionsgeschwindigkeit eine zentrale Rolle. Ebenso die gekoppelte thermische Simulation, um mechanische Bauteillasten zu ermitteln oder auch die akustische Simulation. Weiterhin ist das Einspritzen oder der Zerfall von Sprays ein spannendes CFD-Thema, zu dem es fortschrittliche Modellierungsansätze wie das VOF-to-DPM Model gibt. Um das Vertrauen in die Rechenergebnisse zu stärken, sei außerdem auf zahlreiche Vergleiche mit Experimenten verwiesen [3].
Sie möchten tiefer in all diese Phänomene einsteigen? Führen Sie ein spezielles CADFEM-Training durch, z.B. zu Verbrennung [4] oder auch zu Turbulenz [5]. Denn moderne Simulationsmethoden eröffnen Ingenieuren großartige Perspektiven für schnellere, genauere und effizientere Simulationen, insbesondere für die Nutzung von Wasserstoff in Brennern, Turbinen oder Öfen. Also funktioniert ihr Brenner auch mit Wasserstoff statt Erdgas? Finden Sie es heraus! Mit Simulation und CADFEM!
Seminare zum Thema
-
Praxisgerechtes Vernetzen mit Ansys Fluent Meshing
Im Seminar lernen Sie Geometriedaten vorzubereiten und mit Fluent Meshing in wenigen Schritten Netze zu generieren - auch für komplexe Baugruppen.
-
Verbrennung und reaktive Strömungen mit Ansys Fluent
Lernen Sie, Verbrennungsvorgänge mit CFD zu modellieren, realitätsnah vorherzusagen und weiterzuentwickeln. Diese Schulung wird als 3-tägiges Seminar angeboten.
-
Turbulenzmodelle für typische CFD-Szenarien
In dieser Schulung erlernen Sie die Grundlagen der Turbulenzmodellierung und üben den Einsatz der Modelle in vier praktischen Workshops.
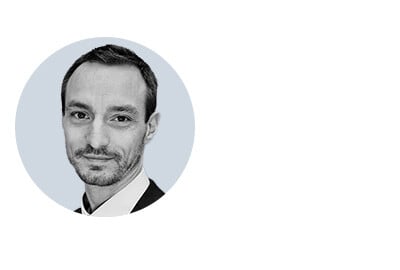
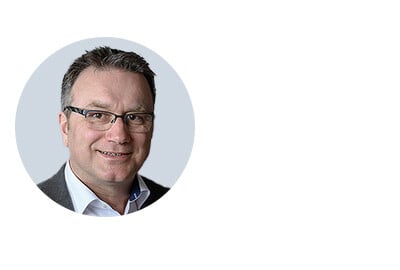
Redaktion
Dr.-Ing. Marold Moosrainer
Head of Professional Development
+49 (0)8092 7005-45
seminar@cadfem.de
Titelbilder: Links © CADFEM GmbH | Rechts: © Adobe Stock
Zuerst veröffentlicht: Januar 2024