Welches ist die richtige Schweißgeschwindigkeit?
Dr.-Ing. Jörg Neumeyer
20.08.2024
TechArtikel 24/13
Schweißprozesse erzeugen viel Wärmeleistung auf möglichst kleinem Bereich, weshalb eine angepasste Prozessführung wichtig ist, um Fehlstellen zu vermeiden und Schweißperlen zu reduzieren – und damit sind insbesondere die auf der Stirn gemeint. Erfahren Sie hier, warum 5 mm/s die richtige Geschwindigkeit für diese Anwendung ist und wie es sogar noch schneller ginge.
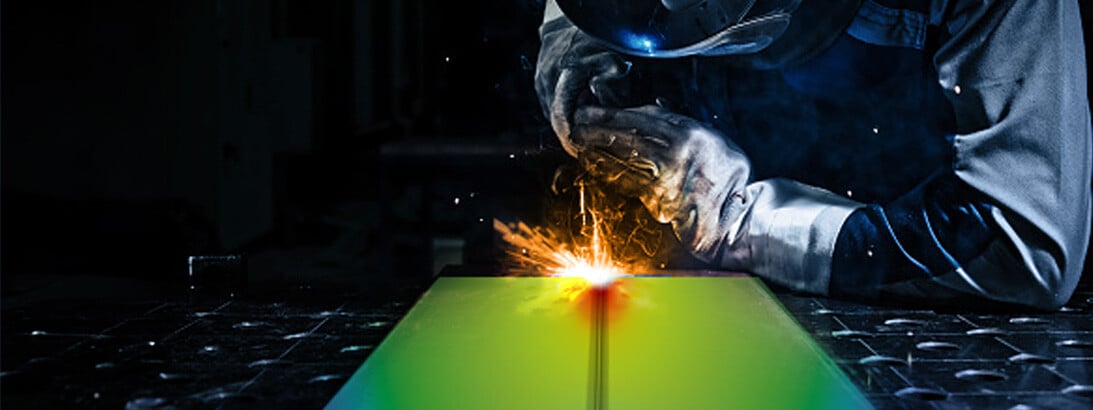
Viel Leistung auf wenig Raum
Schweißprozesse gehören in der metallverarbeitenden Industrie (und mittlerweile auch bei Nicht-Metallen) zu klassischen Zwischenstopps in der Wertschöpfungskette. Die Varianten sind dabei vielfältig und verlaufen vom Elektronenstrahlschweißen in (Fast-)Vakuum über Laserschweißen oder Exoten wie Reibschweißen sowie diverse Atmosphären beim MIG/MAG-Schweißen bis zum Elektrodenschweißen. Das Ziel ist dabei aber gleich: es soll „fokussiert“ Material aufgeschmolzen werden. Das flüssige Material lässt sich entweder leicht entfernen (Trennen) oder es verbindet umliegendes Material (Fügen). Und genau dieses „fokussiert“ bestimmt am Ende die Güte des Prozesses.
So konventionell und historisch etabliert der Prozess selbst ist, so komplex ist die dabei vor sich gehende Physik mit Interaktionen zwischen Temperatur und Mechanik: Schweißverzug - auch oder insbesondere beim Mehrlagenschweißen -, Schmelzbadausbildung, Wärmeeinflusszonen, Gefügeumwandlung usw. Alles beeinflusst sich gegenseitig und zu allem Überfluss auch noch nicht-linear. Gerade bei sicherheitsrelevanten Bauteilen oder hochautomatisierten Vorgängen liegt eine Prozessauslegung nach dem Motto „Et hätt noch immer jot jejange“ (kölsches Sprichwort) irgendwo zwischen „fragwürdig“ und „grob fahrlässig“. Deutlich fundiertere Aussagen zum Prozess lassen sich mit Simulationsmodellen generieren.
In diesem Artikel wollen wir uns ansehen, wie man einen kontinuierlichen Schweißprozess in einem thermischen Simulationsmodell analysieren, auslegen und bestenfalls sogar verbessern kann. Dazu wenden wir einen kleinen Trick an und überführen den realen Prozess mit seiner Bewegung und Zeitabhängigkeit in eine stationäre Simulation - dadurch wird die Auswertung vereinfacht und vor allem die Berechnungszeit minimiert. Letztlich resultiert die maximal zulässige Schweißgeschwindigkeit, sodass eine ausreichende Schweißnahtgüte erfüllt und möglichst hohe Produktivität gewährleistet ist.
Nachlässigkeit in Sicherheitsfragen | © Getty Images
Minimalprinzip: Mit wenig Aufwand viel erreichen
Neben den rein thermischen und strukturmechanischen Eigenschaften kommt noch eine dritte Größe ins Spiel: die Bewegung . In den meisten Fällen bewegen sich Schweißquelle und zu schweißendes Material relativ zueinander. Das Temperaturfeld ist demnach also nicht nur abhängig von den Materialeigenschaften, sondern auch von der Relativbewegung. Spätestens an dieser Stelle wird klar, dass eine Berechnung mit analytischen Ansätzen und Daumenformeln die Realität nur unzureichend treffen kann.
Wir wollen aber für erste Analysen den Ball flach halten und versuchen, möglichst viel Erkenntnis mit möglichst geringem Aufwand zu erhalten. Daher wird der (Laser-)Fokus zunächst auf rein thermische Simulationen gesetzt. Oft reicht bereits das berechnete Temperaturprofil aus, um erste Abschätzungen hinsichtlich der mechanischen Ergebnisse (Spannungen, Verformungen) treffen zu können. Diese ergeben quantitativ nicht unbedingt korrekte Ergebnisse, aber Tendenzen und Worst-Case-Szenarien lassen sich bereits qualifizieren.
Einer der ersten Schritte bei der Erarbeitung eines Simulationsmodells besteht in der Geometrieerstellung. Dazu gibt es heutzutage einen ganzen Blumenstrauß an Tools, die sich jeweils in Optik, Bedienung und Funktionsumfang unterscheiden. Das betrachtete Beispiel wurde in Ansys Discovery erstellt und stellt rudimentär eine Y-Naht dar, welche durch einen Unterpulver-Prozess teilweise aufgefüllt wird. Der Schweißkopf selbst wird durch eine aufgeprägte Wärmeleistung bzw. die im Nachgang existente Schweißverbindung dargestellt. Neben der Geometrie benötigt jedes Simulationsmodell noch Randbedingungen, Lasten und Materialdaten, die in unserem Fall Besonderheiten aufweisen …
Stationäre Temperaturfeldsimulation mit Massentransport | © CADFEM
Gemeinsame Charakterisierung von fest und flüssig
Wir verwenden hier exemplarisch thermische Daten eines Baustahls mit einer Wärmeleitfähigkeit von 60 W/mK, einer Dichte ρ von 7850 kg/m³ und einer besonderen Wärmekapazität cp, die energetisch den Phasenwechsel zwischen fest und flüssig berücksichtigt. Dazu wird dieses cp temperaturabhängig hinterlegt und im Bereich der Schmelztemperatur deutlich erhöht. In der Realität betrifft dieser Kapazitätssprung nur einen sehr kleinen Temperaturbereich. Aus numerischen Gründen wird der Bereich allerdings aufgeweitet. Hier kommt der übliche Kompromiss bei der Simulation ins Spiel: Um den Effekt eines sehr schmalen Temperaturbandes zu berücksichtigen, braucht man sehr viele Elemente und damit viel Geduld.
Anhand von Zahlen lässt sich das Vorgehen verdeutlichen: Wir gehen zunächst von einer konstanten Wärmekapazität von 434 J/kgK aus. Das soll nun bis 1500°C gelten, wo das Aufschmelzen einsetzt. Komplett aufgeschmolzen ist das Material dann bei 1600°C. Die Schmelzenthalpie von Eisen beträgt 275.000 J/kg. Demzufolge entsteht ein Energiebedarf von 434 J/kgK * 100 K + 275.000 J/kg = 318.400 J/kg von Beginn des Aufschmelzens bis zum komplett flüssigen Zustand. Dieser Bedarf wird wiederum auf den relevanten Temperaturbereich verteilt und führt zu einer Wärmekapazität von 3184 J/kgK. Praktisch bedeutet das, dass eine Temperaturänderung in diesem Bereich viel mehr Energie benötigt (Aufheizen) bzw. freisetzt (Abkühlen).
Erinnern wir uns: Wir definieren cp und ρ und sprechen über ZEITLICHE Temperaturänderungen bei Durchlaufen eines Phasenwechsels in einem STATIONÄREN Modell… seltsam, oder? Hintergrund ist, dass ein Advektionsterm meist in der üblichen Schreibweise der Wärmeleitungsgleichung ignoriert wird, weil kontinuierliche Bewegungen ähnlich selten wie der „En-Passant“-Zug im Schach sind. Die Simulation aber kennt diesen Term und erlaubt deshalb Bewegung im stationären Fall. Der Vollständigkeit halber, falls es mal relevant sein sollte: Massentransport könnte auf die gleiche Weise auch in transienten Analysen berücksichtigt werden.
Materialdaten um Umwandlungsenthalpie | © CADFEM
Quick Reference Guide (QRG): Thermische Dehnungen und Spannungen
Erhalten Sie mit dem QRG einen Auszug aus unserer Schulung "Simulation von Temperaturfeldern". Praxiswissen zum schnellen Nachschlagen im Arbeitsalltag, Formeln, Definitionen, Menübefehle und kurze Anleitungen kompakt für Sie aufbereitet. Sie interessieren sich für die gesamte Schulung zum Thema? Hier finden Sie alle Informationen!
QRG kostenlos downloaden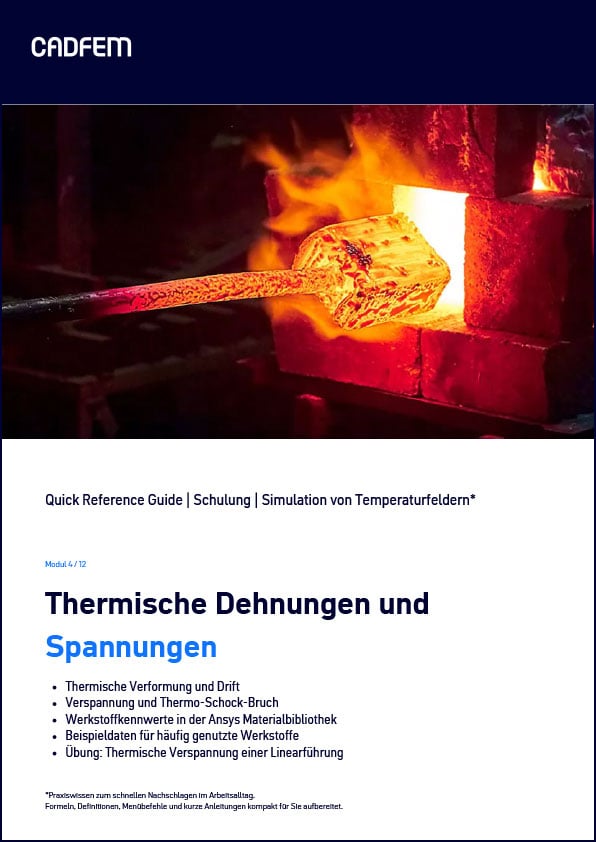
Bewegung im Stillstand
Auch wenn das Simulationsmodell einen kontinuierlichen Prozess abbilden soll, so ist die modellierte Geometrie zunächst begrenzt. Zur Beschreibung des Simulationsprozesses sollte die Temperatur am imaginären Eintrittspunkt des Materials mit einer Temperaturrandbedingung versehen werden. Falls vor dem Erwärmungsprozess kein Bearbeitungsschritt erfolgte, ist hier die Aufbringung der Umgebungstemperatur absolut sinnvoll. Bei der ebenfalls möglichen Betrachtung eines transienten Aufheizprozesses für diese Anwendung könnte auf die Temperaturrandbedingung verzichtet werden und aus solch einer transienten Simulation ließen sich Erkenntnisse gewinnen, wie lang es bis zum stationären Zustand dauert.
Für unsere Simulation werden die klassischen thermischen Randbedingungen (Konvektion, Strahlung, Temperatur am Bereich des Materialeingangs) verwendet. Soweit nichts Besonderes. Richtig interessant wird der Prozess aber bei Implementierung eines Massentransporteffekts. Dazu sind drei Griffe in die Trickkiste nötig. Die Option des Massentransports ist den linearen thermischen Elementen vorbehalten. Daher müssen die entsprechenden Körper mit Elementen ohne Mittenknoten vernetzt werden. Als Nächstes brauchen die Komponenten eine Umschaltung der Keyoption Nr. 11 auf den Wert 1 und eine Definition sogenannter Real-Konstanten. Falls nur ein Elementtyp verwendet wird, reicht der der Zweizeiler aus der Abbildung.
Und der dritte Kniff besteht in der Zuweisung einer Geschwindigkeit zu den zugehörigen Berechnungsknoten mittels eines APDL-Codes. Die Geschwindigkeit von 5 mm/s in y-Richtung ist dabei in Relation zum globalen kartesischen Koordinatensystem zu definieren. Das heißt wiederum, dass für rotatorische Bewegungen, welche im schlimmsten Fall nicht einmal um eine der Koordinatenachsen verlaufen, ein Rückgriff auf den ggf. längst vergessenen Mathematikunterricht mit Trigonometrie und Koordinatentransfer nötig ist. Zugegeben: Das klingt nach Raketenwissenschaft, aber Sie können anhand der Abbildung sehen, dass es wirklich kein Hexenwerk ist und die Funktionalität rechtfertigt letztlich den Aufwand!
Temperaturverteilung bei kontinuierlichem Vorschubprozess | © CADFEM
Vom bunten Bild zum Erkenntnisgewinn
Die Temperaturfeldsimulation zeigt unter Berücksichtigung von eingebrachter Leistung, Massentransport und Randbedingungen plausible Ergebnisse. Für die hier verwendete Geometrie wird eine effektiv eingebrachte Wärmeleistung von 400 W verwendet. Eine freie Konvektion an die Umgebung mit 5 W/m²K sowie ein Emissionskoeffizient von 0,9 definieren neben einer konstanten Temperatur von 22°C am Eingangsbereich des Blechs die thermischen Randbedingungen. Die hierbei wichtigste Frage betrifft die Geschwindigkeit des Vorschubs, da sie als variabler Eingangsparameter zur Verfügung steht, die Verteilung des Temperaturfeldes stark beeinflusst und entsprechend unterschiedliche Ergebnisbilder generiert.
Nun sind die gewonnenen bunten Bilder zwar an sich schön anzusehen, aber viel relevanter sind die Prozesseigenschaften, die sich aus der Simulation ableiten lassen. Bei einer sehr fokussierten Wärmeeinbringung wie bei Schweißprozessen sind die sogenannten Wärmeeinflusszonen (kurz: WEZ) von hohem Interesse, da sich dort aufgrund von Kornwachstum, rekristallisierten Zonen usw. Schwachstellen im Material einstellen. Diese Schwachstellen zeigen sich in korrosionsanfälligen Bereichen, Schweißrissen oder generell verminderten Festigkeiten.
Zur Auswertung eignen sich hierzu Schnittbilder des Temperaturfeldes und Pfade entlang der definierten Vorschubrichtung. Während die Schnittbilder eine Aussage zu den Temperaturverteilungen im Material machen können, eignen sich Pfade hervorragend, um Temperaturverweilzeiten und -maxima in Abhängigkeit verschiedener Materialtiefen zu extrahieren. Klingt vielleicht erstmal seltsam, dass aus einer stationären Analyse Ergebnisse zu Verweil-ZEITEN abgeleitet werden können, oder? Aber letztlich kann die Temperatur-Länge-Auswertung über die konstante Vorschubgeschwindigkeit auf eine Temperatur-Zeit-Auswertung umgerechnet werden. Und somit zeigen die Pfade, wo und WANN die jeweilige Temperatur erreicht wird.
Pfadauswertung 0,4 mm unter der Oberfläche bei 5 mm/s | © CADFEM
So schnell wie möglich
Eine hohe Prozessgeschwindigkeit führt zu einer kleinen Einwirkzeit und damit einer geringen Energie-, also Wärmeeinbringung, was nicht akzeptabel ist. Kleine Geschwindigkeiten verringern die Produktivität und damit den Umsatz und können unter Umständen zu unzulässig hohen Temperaturen führen, was ebenfalls nicht akzeptabel ist. Für eine Geschwindigkeit von 5 mm/s hat sich bei den gegebenen Lasten und Randbedingungen ein guter Kompromiss aus möglichst hoher Produktivität und ausreichend hoher Temperatur ergeben. Was kann man aber tun, wenn es noch etwas schneller sein soll, aber kein stärkerer Schweißprozess verfügbar ist?
Der Temperatursprung von Raumtemperatur auf Schmelztemperatur ist groß und damit energieintensiv. Wie wäre es also, wenn man die Sprunghöhe durch eine Vorerwärmung des Blechs verringert? Die betrachteten Bleche haben den charmanten Vorteil, dass sie metallisch sind – meist sogar ferromagnetisch – und damit hervorragend durch einen induktiven Erwärmungsprozess vorerwärmt werden können. Das funktioniert berührungslos und sorgt gleichzeitig auch noch für eine Erwärmung des umliegenden Bereichs, was die Temperaturgradienten reduziert und damit mechanische Spannungen aus dem System nimmt. Auch das lässt sich mit Simulation untersuchen und hier wurden 160 W über Induktion zusätzlich in das Blech eingebracht.
Kombiniert man nun also Induktion und Strahlschweißprozess, so lässt sich mehr Leistung im prozessrelevanten Bereich einbringen. Und wenn mehr Leistung verfügbar ist, benötigt man nicht so viel Zeit, um auf eine bestimmte Mindesttemperatur im Schweißbereich zu kommen – wir können also schneller schweißen! In unserem Fall ergibt sich eine Geschwindigkeitserhöhung von 40% mit dem charmanten Nebeneffekt der reduzierten thermisch induzierten Spannungen. Und wem das noch nicht reicht: Mit Simulation können auch Kombinationen aus Laser und Lichtbogen oder pendelnde Schweißquellen usw. analysiert und hinsichtlich einer Prozessverbesserung quantifiziert werden.
Minimaltemperatur im Schweißbereich über der Vorschubgeschwindigkeit | © CADFEM
Seminare zum Thema
-
Simulation von Temperaturfeldern
Lernen Sie, thermische Analysen in Ansys Mechanical durchzuführen: Best Practice zu Heiz- und Kühlaufgaben sowie Ermittlung thermischer Spannungen. Diese Schulung wird als 3-tägiges Seminar angeboten oder alternativ als eLearning-Kurs mit freier Zeiteinteilung.
-
Let's simulate - Temperaturfeld mit Vorschub
Schweißen ohne Schweißperlen - Dr.-Ing. Jörg Neumeyer und Dr. rer. nat Sigrid Lang diskutieren an Simulationsbeispielen wie Wärme- und Massentransport in Festkörpern und Fluide abgebildet werden können. Mit den hilfreichen Tipps und der korrekten Anwendung der Gleichungen sowie der gezeigten Heransgehensweise für stationäre Temperaturfeldberechnungen sind Sie nach dieser Serie in der Lage das Temperaturfeld aufgrund eines Schweissprozesses zu simulieren. Und deswegen ist diese Serie ein Muss für alle Ingenieure, die ihr Wissen in der Temperaturmessung und -simulation vertiefen möchten.
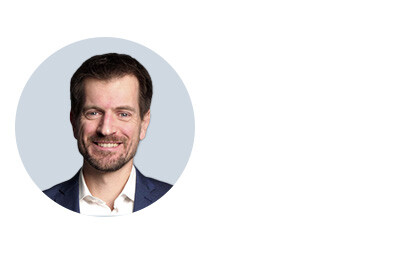
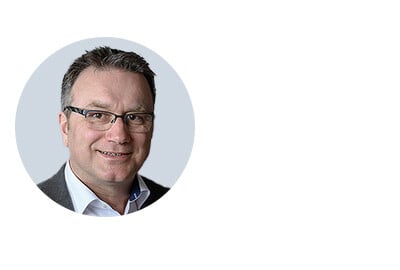
Redaktion
Dr.-Ing. Marold Moosrainer
Head of Professional Development
+49 (0)8092 7005-45
mmoosrainer@cadfem.de
Titelbild: © CADFEM GmbH / Getty Images